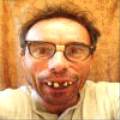
Herr Ball
Just thought I would tell everyone about a great experience I had yesterday.
I have been keeping up with all the treads about Dimension Engineering's Kangaroo in here, as trying to keep my robot on a straight path has not been very successful. Now that Tony has been working with it and adapted it to the V4 I thought it was time to take the plunge. No need to order it off the net, I only live about 10 minutes from where it's sold, so off I went for a drive. So glad I did! I walked into the business and was greeted by a very nice and polite young lady ( very pretty too ...lol). Anyways, I asked to purchase a Kangaroo and she went and got one. Well as she was ringing up my bill I began a conversation asking her if they assembled the Dimension Engineering items here. She said we not only assemble them here but make them as well. Wait I said, electronic items actually made here in the states. She said they make everything they can here, even machining there own heat sinks for the items. She then asked if I would be interested in taking a tour around the place. Interested, I kill for a tour! She took me all around showing me every machine explaining each. I was in heaven as we went from one to another. It was amazing to see how boards are built and the machines it takes to do it. Then as we past a very young looking guy she introduced me and said this is the owner. Owner, I was blown away that such a young guy could be the owner of such a great company. (Later when leaving I mentioned I can' believe a guy as young as you can own all this, his reply, well I'm not as young as I look, I'm 33 ... LOL.) I ask who was the developer of the Kangaroo and he said he was. I told him that the guys on the EZB forums talked very highly about the Kangaroo and thanked him for his help a couple of time that he posted. He said he would like to do more of that but running the company takes up most of his time. I said that's understandable. He then said he had to get back and thanked me for coming. After looking at all the assembly machines she took me to the machine shop and showed me how it worked. Getting ready to leave and say goodbye she asked if I had ever heard of a company called Tiny Circuits, yes I said, and she told me that company is own by her husband and if I ever wanted to tour it she would ask him to show me around. It was really a great experience and as I was driving home I was almost on a high ... LOL.
I have for the past several years been very interested in electronics from circuit designs to how it all comes together. Seeing exactly how it works, or at least the assembly part was pretty cool.
Hope I didn't bore anyone here, just wanted to share with someone that might appreciate it like me.
Herr
P.S. I now see they have spell checking here, GREAT idea!
What a way to shop for what you wanted and also get to see how it is made. Very Nice !
I also have had good experience from dimension engineering. They are positive people like ez robot and we're happy to talk about my project and equipment needs. I would recommend them
DE didn't even acknowledge a single email I sent them regarding the Sabertooth or Kangaroo... take from that what you want
@Herr Ball, (can I call you Ted?) What a great opportunity to meet Dimension Engineering they seem to be a really great company, the developer of the Kangaroo that you met must be a real genius! as the product is a fantastic piece of engineering. For me, its the autotune function that flies it miles ahead of anything else, also the DEscribe software is easy to use and very useful. I wonder if @James Bellinger who has posted here on the forum is this developer? I suspect he is.
I currently have a major tech problem with the Kangaroo as in my tests here it only gives me around half max speed in mixed mode (compared to independent mode) the DE technical support have been great and are looking into the situation for me, I am most satisfied with their level of support and service, but unfortunately we have not solved the problem yet.
I am desperate to try to get a solution to this problem as I really want to use the Kangaroo/Sabertooth combo into the production EZ:2 robots, but if it cannot be solved I will have to go back to the Motormind 3 or try the Roboclaw controllers which also have PID fuctions.
In conclusion, I think Dimension Engineering is an exciting innovative company (like EZ-Robot) and set to go places and I would recommend their products.
Tony
Thanks for the report. Next time photo or video too, please...
j
@jdeBay.... "Next time photo or video too, please" .... you sound so demanding with that statement.... Tony has other things to do....
Thanks for sharing your wonderful trip with us. We saw it through your eyes.
It was Great!
@Herr, What luck and fun! Where are they located? I had no idea they were a smaller company. This explains why it sometimes hard to get support or deep helping answers. If the owner is one of the only ones responsable for customer support, keeping the company running and R&D then I bet he is overwhelmed most of the time. Still to have them stop and give you the grand tour says a ton about the mind set of the company and what they think about the user.
DE's line of product is excetional and dam near bullit proof. I use two Sabertooth/Kangaroo combo boards in my B9 and plan to add a third at some point. Once dummies like me get past the learning curve and get it set up properly it really is quite easy to run. I do hope they are able to "strighten" the curve a little more so it would not be as diffacult to set up and understand for the new user. Perhaps a Sabertooth/Kanagroo for Dummies approch in their manuls and a user forum like EZ Robot has.
@Tony, I truly hope they can find the cause of the half speed problem. It would be a shame to have to go to a different drive system. I think I read somewhere when I was settting up my boards and trying to overcome problems I was causeing about this problem and a fix (hopefully) on a forum somewhere. I'll have to go back and look. It should not be too hard to find as there isn't much out there on the web conserning Kangaroo x2. I was having setup problems like the Kangaroo loosing the tune and not starting if I stopped it over night next to a limit switch. I would have to retune it each morning. Turns out the battery would keep the Kangaroo/Sabertooth powered up after I shut down the robot, slow trickle down to dead and that whiped the memory in the kangaroo. I had to make sure the kangaroo was also disconnected from the battery at the same time the robot was powered off and all was well after that. DE was right there with many emails and suggestions but my trial and error found the right solution. I dont know what the message to you is in my experance but it may help somehow.