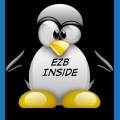
Darathian
USA
Asked
— Edited
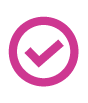
Is there any way to control the speed of the continuous rotation servo's from the developers kit via the mobile interface?
I tried a few different controls but none seem to work. I also tried the servo speed command
They move like their trying to win a speed race.
Thanks
You should be able to adjust via "PWM (digitalPort, speed)" in the script configuration of a given directional control. So if you add a forward button, add PWM script controls for both drive motors and set the speed.
You could add a second set of controls for another speed level. One set for fast. One set for slow.
Thanks for the answer.
By PWM control do you mean the PWM slider control?
I tried that and got some reaction from it but it's going from super fast at a specific duty cycle to super slow, to reverse.
The servo speed control does nothing.
Thank
So changing the numbers in the modified servo Movement Panel had no effect on servo speed at all?
@Darathian - no, not the slider control. Try this, add a forward button. Then select the button...and off to right do you see where it says "On Pressed Script" and by default it says "Forward()". Well next to that is a pencil icon. Click on the pencil. This opens up the script interface...now you have to make a script and add "PWM (digitalPort, speed)" . You'll need two script lines one for your right and left drive motor.
@Richard I don't think there is Modified servo Movement Panel in the mobile interface. Unless its hidden? I bet you guys hide it in my version
Ok, just figured he might get it working in ARC before trying to move it to his Android device...
Hey guys, I just did a little test this morning which will help everyone trying to slow down their 360° Servos.
Using the "Modified servo Movement Panel" Control, in the settings enable the "use" check box beside the Stop value. You will then likely have to change your Stop values from the default value of 89 to something else. Take the opportunity to save your changes and then test them by clicking on the directions and stop buttons within the Modified servo movement panel. Then adjust the Forward and Reverse values to be close to the center value of your servos in order to slow the servos down, the closer to the stop value they are the slower the servos will go.
Here's the settings I used:
Keep in mind your servos may be slightly different on the center ("stop") values than my example due to the nature of 360° Servos (different potentiometer values). You also may have to tweak the forward and reverse values on the servos to keep your robot tracking straight. Servos often spin faster one way than the other so when you use 2 x 360° Servos mounted in opposite directions they naturally tend to make the robot favor turning instead of going straight. One direction will be of a value further away from the stop value than the other.
I can confirm that once these settings are saved they work in the mobile interface as well.
@Jeremie Please note that this is for v4 servos from the development kit NOT v3 servos. I tried setting on version 3 servos, works very very slow...
John
The numbers for the V3 kit servos are different, but the concept is the same. The speed is controlled by the forward and reverse values. I had to set mine to different values because one of my servos spins a little faster than the other so my bot would slowly go in circles (and of course, they are backwards from each other when actually mounted on a bot, so you would flip the forward and reverse values for left and right servo).
Alan