
guffi210191
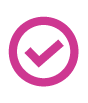
Hi everyone,
I am currently trying to present and hopefully sell EZ-robots to schools in the middle east. We have been using the robots for 3 months now and we go to different meetings and demonstrations with the robots to gain some attention.
But we have a problem: Burned out servos. At the moment we are having troubles with 5-6 different servos. They simply stop working or snap in the middle of movements. Last time we were at a demo, JD's arm suddenly broke and went the wrong way during a pushup script. We immediatly replaced the servo with another one, but now the problem is that SIX is only working as spare-parts.
I would like to know if some of you guys are facing the same problem with burned out servos? we have tried to open up a few of them, to check for mistakes and on one of them, the chip is melted. On two of the others, the motor is working just fine when we connect it to 6V batteries, but they don't move when connected to the chip, even though nothing appear to be wrong. On the last 2-3 nothing happens, so we suspect that the motors are burned out.
To me it just seems too fast with these burn-outs, because if we are selling them to schools, they should be working for a long time.
Kind regards, Benjamin
I
are you callibrating the servo's?
Yes, we always callibrate the servo's. The problem always appears, when we are running actions, both the ones included in the software, but also the ones we make ourselves.
I used two six's, a jd and a roli, along with 3 dev kits this school year with 4th and 5th grade students who had never been exposed to robotics before. Here are all of the issues that we had and the causes for each.
1 mini servo burned out in JD'S hand. Cause was the calibration step not being completed and the hand trying to closed even when it was already closed.
1 battery failure when a student decided to spin the battery that was connected to the barrel connector causing the + and - battery posts to make contact. Unfortunately, this contact was mad really well when the student then plugged in the EZB. The EZB survived which is amazing, but the battery swelled as sparks and smoke started shooting out front the connection. I grabbed wire cutters and cut one of the battery wires to kill the issue.
one mini servo in the neck of JD went out. This was because the students at this age really enjoy moving jd by hand even when the robot is in use.
JD shoulder servo went out due another servos wire being caught when running, causing the servo not to be able to move.
The student who caused these issues was removed from the class after the battery issue. Oddly enough, all of the issues stopped.
All of these robots were some of the first ones released of these. I did spend some time about half way through the school year going over each robot to make sure everything was working on them correctly. I would say that in the beginning it is important to do this about once a week until the students become comfortable with the robots and quit trying to use them like dolls instead of robots. I would also say that it would be smart to buy a couple of extra servos anyway because servos do go out. It would also be wise to buy new batteries every year and have a teacher who is willing to become proficient with robotics.
Realistically, you are talking about $500 per robot. That cost is nothing compared to the other options. Also, the platform blows away anything else out there that costs 4 to 5 times as much. If you have had 6 servos go out while doing shows, I would say that you haven't done the calibration step. Also, that is about $100 including shipping. Still a far better deal than the alternatives.
Edit - while I was typing this, you posted that you had done the calibration step. I would revisit it again as it sounds like it wasn't completed correctly. It's kind of hard to have the results that you describe when having a properly calibrated robot.
Thank you very much for your respond d.cochran. When we do demos we are standing next to the robots all the time and almost nothing has gone wrong. Only issue is that JD sometimes fall over.
When we power on the robots, we always start up by callibrating them, so arms and legs are completely straight. As I said we have been using these robots for quite some time and yep - servos do break. But I still think this is too fast. The problem is that when we are treating them nicely and these things happen, then I dont know what will happen, if we give them to students who don't know much about robots.
We have tried to copy the "Pushups" movement with JD and I am suspecting that creating your own actions is part of the problem. Maybe some of the movements are happening too fast for the servos to follow - but if so, I would say that the EZ-software should limit the speed.
you can use the contact ,us and paste this topic.
you can also set the speed off servo's. excample (d4,1) one is fast -10 slow.
@nomad.
You got it back to front. "1" is fast and "10" is very slow (and 0 is servo release).
@guffi210191.
I have had a couple of servos burn out for no apparent reason (no excess weight, no snagged wires, ect), but with the amount I have used, it's like 1 in 30, and servos a bought a year ago are still working. Sorry to hear your having problems though.
hi steve G
where?hahaha thanks for correcting that.
I am in contact with the EZ-team now, But thank you for all your answers.