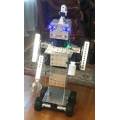
PRO
EzAng
USA
Asked
— Edited
In "auto position" control, how do I distinguish one D0 from the other D0 on the same connection (connect 0 to 4)?
I am using a vertical servo control and a horizontal servo control on the same I/0 port D0
EzAng
Related Hardware EZ-B v4
Related Control
Auto Position Movement Panel (Gait)
I don’t understand the question. Every skill control has a board index option, including every servo setting in the auto position.
In the Auto Position control, how do I distinguish between a vertical servo D0 and and a continuous servo D0? - I am using both on my robot
on the same connection (connect )
Here is a pic of the arms, notice it has 2 parts
thanks EzAng
You don't - a horizontal servo is a horizontal servo skill. It is just a skill for controlling a servo. It has nothing to do with any other control that controls servos. Read this document: https://synthiam.com/Docs/ARC-Overview/Servo-Controls
Any servo connected to D0 is a servo on D0. The Auto Position has it's own servo control. The horizontal servo skill has it's own servo control. The camera has it's own servo control. Every skill is not dependent on any other skill.
You can delete the horizontal and vertical skills and the Auto Position will still work.
What do you mean it has two parts? You can only connect 1 (one) servo to a port. D0 is a port. You connect a servo to a port, which is D0. You select that port and control the servo.
Also, you may press the ? (question mark) next to the X (close) button on the vertical or horizontal skill control to view help. Here's a direct link to the manual page for the vertical servo skill: https://synthiam.com/Docs/Skills/Servo/Vertical-Servo?id=16095
In the Auto Position config, you can see a number before the port. That number is the board index. In this example, take a look at the number 0 and number 1 before the D0. Meaning, board index 0 and board index 1.
To select the port and board index, select the servo port button and edit the config. This is the same for ALL robot skills that use servos across ARC entirely. It's documented in the link I pasted above about how servo controls work.
I am trying to explain my problem:
I use a continuous servo D0 because it has a "stop" function so the arm doesn't keep moving
The vertical servo D0 does not have a "stop" function, it just has a slider (probably wrong term)
I need both to control movement
I hope I am explaining myself clearly
EzAng
I still do not fully understand. What I believe to understand, any servo connected to D0 is the same servo. Please follow the manuals, which explain in greater depth what I'm repeating
I understand your pictures and the manual
Now what do you do when you have "two" D1s and D2s?