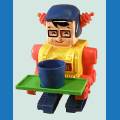
Mulberry
USA
Asked
— Edited
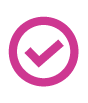
Afternoon All
Can anyone confirm the H Bridges in the tutorials are still not suitable for 12 volt motors even with the new EZ boards? I want to avoid the headache of using a Pololu H bridge. The wiring and configuration are a nightmare This is for a simple waist rotation, not high speed.
Thanks,
Daniel
The question with an H-brisdge is always amps not volts (well , not entirely, but virtually any H-bridge on the market can easily handle 12 volts). We need to know how many amps the motors draw at stall, then you add a percentage for good measure, and that will tell you what to get.
The EZ-B store has an easy to use 2.5 amp controller (although it requires 6 digital ports for 2 motors with PWM). Sabertooth has H-bridges that support from 5 to 60 amps and just use one digital port since they use a serial protocol. For a single motor, you can also look at R/C escs.
Alan
The Pololu H bridges work (I actually had one going last year) but I've been unable to get any others to work. I've gone through 4 (and they aren't cheap) just for this one function. The issue is either my soldering and/or port connections. At least with the bridge in the tutorials the directions are clear. With any other H bridge I'm flying blind.
Daniel
As Alan has said, it's not the voltage you need to consider so much, it's the amps again (as explained in your servo thread). Just to add, as well as the stall draw, the weight of what the motor is moving as well (in your instance, the weight from the waste upwards). There are 10, 15, and 20 amp motor controllers with H-Bridge available on eBay and Amazon which are reasonably priced and not that much different to wire up than the L298 H-Bridge.
I know because I did exactly this for two 12v drive motors. Bench testing the motors drew 1.2 amps. Stalling the motors (physically holding them with my hand) spiked to 2.1 amps. Fitted to the chassis with the full weight of the robot on top, when driving the motors drew 2.4 amps with a stall spike of 5 amps. A two channel £20 ($35) 10 amp motor controller fixed my issues and still works well today (no soldering required). If your using one motor, a single channel H-Bridge is all you need which should be cheaper.
So to answer your initial question, you can in fact use the H-Bridge in the tutorials with 12 volt motors, but it depends how many amps the motors draw. Test the amp draw with a multi meter. If you don't have one you should get one as they are a good investment.
Motor controller I currently use.
Wiring for the H-Bridge motor controller I linked to in the above post. As mentioned this is a two channel H-Bridge motor controller for two motors, but one motor can be used.
I have a related question, if i may. I'm using the H bridge that EZ-R sells and it works very well. I am using the the EZB battery (7volt +-) . Is it ok to use a separate 12vdc battery and just tie the grounds together? My motors are 12 volt as well and just run a little slower with the lower voltage. (current isn't a problem).
@Steve B, yes, that is the main purpose of an H bridge, providing different voltage and/or amps than the signaling device (EZ-B in this case) can handle.
Alan
@ Alan Thanks! I was pretty sure that that was the case. I'm just a little gun shy...this is my second h-bridge, eek
@SteveB.
Don't worry about being a lil gun shy. I was exactly the same as you when I wired my first H-Bridge controller up (the one in the pics above). As you say, as long as you have the common ground in place and the little white regulator button in the correct position (I think it's push down), then your golden.