What in the world am I making?! I’ll post pics as I go
Community General What am I making? jstarne1 USA Asked Apr 2023 What Am I Making? Skip to comments Jump to end What in the world am I making?! I’ll post pics as I go Jump to end Upgrade to ARC Pro Harnessing the power of ARC Pro, your robot can be more than just a simple automated machine. Compare Pro Features View Subscription Plans jstarne1 USA #1 Apr 2023 2 An IOT EZ Board in here.. DJ Sures PRO Synthiam #2 Apr 2023 Oh this will be fun! I like guessing games jstarne1 USA #3 Apr 2023 — Edited Apr 2023 I soldered on long pigtails and a charging port for this 6v usb charger. No need to use a large specialized charger on this little robot. jstarne1 USA #4 Apr 2023 1 6-12v spur gear motors get their pig tails and heat shrink. I am surprised at how quietly they run. Spur gears are known to make a wining whizzing noise. DJ Sures PRO Synthiam #5 Apr 2023 — Edited Apr 2023 I keep seeing those antenna-looking things in the back on the piece of wood. Oh, and where did you get those tracks from? they look heavy-duty and real modular jstarne1 USA #6 Apr 2023 This is a track kit from Amazon.com https://www.amazon.com/gp/aw/d/B094N8DHVR?psc=1&ref=ppx_pop_mob_b_asin_title https://www.amazon.com/SZDoit-Chassis-Stainless-Platform-Raspberry/dp/B07F41G9Z6/ref=sxin_22_pa_sp_phone_search_thematic_sspa?content-id=amzn1.sym.1ad53d03-de9d-4733-8030-19769ee35352%3Aamzn1.sym.1ad53d03-de9d-4733-8030-19769ee35352&crid=2O8QTTODWN37K&cv_ct_cx=tank+arduino+kit&keywords=tank+arduino+kit&pd_rd_i=B07F41G9Z6&pd_rd_r=ce7e3af1-729d-4f1c-a840-bd1370df12c0&pd_rd_w=yFpR7&pd_rd_wg=9ZcfV&pf_rd_p=1ad53d03-de9d-4733-8030-19769ee35352&pf_rd_r=J3CTBT24AM1DDMVKM9P6&qid=1681967451&sbo=RZvfv%2F%2FHxDF%2BO5021pAnSA%3D%3D&sprefix=tank+arduino+kit%2Caps%2C92&sr=1-3-a73d1c8c-2fd2-4f19-aa41-2df022bcb241-spons&psc=1&spLa=ZW5jcnlwdGVkUXVhbGlmaWVyPUFCS0c4UllTV09GTFImZW5jcnlwdGVkSWQ9QTA4NDUwMjlESzNKWDBHN0JBTEUmZW5jcnlwdGVkQWRJZD1BMDkwMTM0OTJPODdJREFRVU9RSUsmd2lkZ2V0TmFtZT1zcF9waG9uZV9zZWFyY2hfdGhlbWF0aWMmYWN0aW9uPWNsaWNrUmVkaXJlY3QmZG9Ob3RMb2dDbGljaz10cnVl https://www.amazon.com/Professional-Chassis-Platform-Accessory-Raspberry/dp/B08YFG42QH/ref=mp_s_a_1_37?crid=2O8QTTODWN37K&keywords=tank+arduino+kit&qid=1681967579&sprefix=tank+arduino+kit%2Caps%2C92&sr=8-37 https://www.amazon.com/Processional-Raspberry-Microbit-Avoiding-Obstacle/dp/B09KL2DP68/ref=mp_s_a_1_41?crid=2O8QTTODWN37K&keywords=tank+arduino+kit&qid=1681967579&sprefix=tank+arduino+kit%2Caps%2C92&sr=8-41 https://www.amazon.com/Professional-Absorption-Suspension-Supporting-Raspberry/dp/B09KLH5SKX/ref=mp_s_a_1_42?crid=2O8QTTODWN37K&keywords=tank+arduino+kit&qid=1681967579&sprefix=tank+arduino+kit%2Caps%2C92&sr=8-42&ufe=app_do%3Aamzn1.fos.006c50ae-5d4c-4777-9bc0-4513d670b6bc Hear are stand alone track kits https://www.amazon.com/SZDoit-Plastic-Chassis-Arduino-Learning/dp/B08J3ZSVGM/ref=mp_s_a_1_10_sspa?crid=4WGBPFJWLADR&keywords=arduino+tank+kit&qid=1681967788&sprefix=arduino+tank+kit%2Caps%2C86&sr=8-10-spons&psc=1&spLa=ZW5jcnlwdGVkUXVhbGlmaWVyPUEyM1BWRUQ5VlFYVE9PJmVuY3J5cHRlZElkPUEwNTU0NjY0VzlNSDBaVTE1UDhJJmVuY3J5cHRlZEFkSWQ9QTA5MDE3NDkxSUNQT1RWMjJIQk9IJndpZGdldE5hbWU9c3BfcGhvbmVfc2VhcmNoX210ZiZhY3Rpb249Y2xpY2tSZWRpcmVjdCZkb05vdExvZ0NsaWNrPXRydWU= jstarne1 USA #7 Apr 2023 Oh the antenna dudes are magnetic arms to hold wires while soldering, the yellow base is a iron plate making some room for a servo, TaDa! jstarne1 USA #8 Apr 2023 I’m sketching out the next part to 3D print, a servo to EZ bit camera adapter 1 2 3 » »» Login to post a comment
jstarne1 USA Asked Apr 2023 What Am I Making? Skip to comments Jump to end What in the world am I making?! I’ll post pics as I go Jump to end
jstarne1 USA #3 Apr 2023 — Edited Apr 2023 I soldered on long pigtails and a charging port for this 6v usb charger. No need to use a large specialized charger on this little robot.
I soldered on long pigtails and a charging port for this 6v usb charger. No need to use a large specialized charger on this little robot.
jstarne1 USA #4 Apr 2023 1 6-12v spur gear motors get their pig tails and heat shrink. I am surprised at how quietly they run. Spur gears are known to make a wining whizzing noise.
6-12v spur gear motors get their pig tails and heat shrink. I am surprised at how quietly they run. Spur gears are known to make a wining whizzing noise.
DJ Sures PRO Synthiam #5 Apr 2023 — Edited Apr 2023 I keep seeing those antenna-looking things in the back on the piece of wood. Oh, and where did you get those tracks from? they look heavy-duty and real modular
I keep seeing those antenna-looking things in the back on the piece of wood. Oh, and where did you get those tracks from? they look heavy-duty and real modular
jstarne1 USA #6 Apr 2023 This is a track kit from Amazon.com https://www.amazon.com/gp/aw/d/B094N8DHVR?psc=1&ref=ppx_pop_mob_b_asin_title https://www.amazon.com/SZDoit-Chassis-Stainless-Platform-Raspberry/dp/B07F41G9Z6/ref=sxin_22_pa_sp_phone_search_thematic_sspa?content-id=amzn1.sym.1ad53d03-de9d-4733-8030-19769ee35352%3Aamzn1.sym.1ad53d03-de9d-4733-8030-19769ee35352&crid=2O8QTTODWN37K&cv_ct_cx=tank+arduino+kit&keywords=tank+arduino+kit&pd_rd_i=B07F41G9Z6&pd_rd_r=ce7e3af1-729d-4f1c-a840-bd1370df12c0&pd_rd_w=yFpR7&pd_rd_wg=9ZcfV&pf_rd_p=1ad53d03-de9d-4733-8030-19769ee35352&pf_rd_r=J3CTBT24AM1DDMVKM9P6&qid=1681967451&sbo=RZvfv%2F%2FHxDF%2BO5021pAnSA%3D%3D&sprefix=tank+arduino+kit%2Caps%2C92&sr=1-3-a73d1c8c-2fd2-4f19-aa41-2df022bcb241-spons&psc=1&spLa=ZW5jcnlwdGVkUXVhbGlmaWVyPUFCS0c4UllTV09GTFImZW5jcnlwdGVkSWQ9QTA4NDUwMjlESzNKWDBHN0JBTEUmZW5jcnlwdGVkQWRJZD1BMDkwMTM0OTJPODdJREFRVU9RSUsmd2lkZ2V0TmFtZT1zcF9waG9uZV9zZWFyY2hfdGhlbWF0aWMmYWN0aW9uPWNsaWNrUmVkaXJlY3QmZG9Ob3RMb2dDbGljaz10cnVl https://www.amazon.com/Professional-Chassis-Platform-Accessory-Raspberry/dp/B08YFG42QH/ref=mp_s_a_1_37?crid=2O8QTTODWN37K&keywords=tank+arduino+kit&qid=1681967579&sprefix=tank+arduino+kit%2Caps%2C92&sr=8-37 https://www.amazon.com/Processional-Raspberry-Microbit-Avoiding-Obstacle/dp/B09KL2DP68/ref=mp_s_a_1_41?crid=2O8QTTODWN37K&keywords=tank+arduino+kit&qid=1681967579&sprefix=tank+arduino+kit%2Caps%2C92&sr=8-41 https://www.amazon.com/Professional-Absorption-Suspension-Supporting-Raspberry/dp/B09KLH5SKX/ref=mp_s_a_1_42?crid=2O8QTTODWN37K&keywords=tank+arduino+kit&qid=1681967579&sprefix=tank+arduino+kit%2Caps%2C92&sr=8-42&ufe=app_do%3Aamzn1.fos.006c50ae-5d4c-4777-9bc0-4513d670b6bc Hear are stand alone track kits https://www.amazon.com/SZDoit-Plastic-Chassis-Arduino-Learning/dp/B08J3ZSVGM/ref=mp_s_a_1_10_sspa?crid=4WGBPFJWLADR&keywords=arduino+tank+kit&qid=1681967788&sprefix=arduino+tank+kit%2Caps%2C86&sr=8-10-spons&psc=1&spLa=ZW5jcnlwdGVkUXVhbGlmaWVyPUEyM1BWRUQ5VlFYVE9PJmVuY3J5cHRlZElkPUEwNTU0NjY0VzlNSDBaVTE1UDhJJmVuY3J5cHRlZEFkSWQ9QTA5MDE3NDkxSUNQT1RWMjJIQk9IJndpZGdldE5hbWU9c3BfcGhvbmVfc2VhcmNoX210ZiZhY3Rpb249Y2xpY2tSZWRpcmVjdCZkb05vdExvZ0NsaWNrPXRydWU=
This is a track kit from Amazon.com https://www.amazon.com/gp/aw/d/B094N8DHVR?psc=1&ref=ppx_pop_mob_b_asin_title https://www.amazon.com/SZDoit-Chassis-Stainless-Platform-Raspberry/dp/B07F41G9Z6/ref=sxin_22_pa_sp_phone_search_thematic_sspa?content-id=amzn1.sym.1ad53d03-de9d-4733-8030-19769ee35352%3Aamzn1.sym.1ad53d03-de9d-4733-8030-19769ee35352&crid=2O8QTTODWN37K&cv_ct_cx=tank+arduino+kit&keywords=tank+arduino+kit&pd_rd_i=B07F41G9Z6&pd_rd_r=ce7e3af1-729d-4f1c-a840-bd1370df12c0&pd_rd_w=yFpR7&pd_rd_wg=9ZcfV&pf_rd_p=1ad53d03-de9d-4733-8030-19769ee35352&pf_rd_r=J3CTBT24AM1DDMVKM9P6&qid=1681967451&sbo=RZvfv%2F%2FHxDF%2BO5021pAnSA%3D%3D&sprefix=tank+arduino+kit%2Caps%2C92&sr=1-3-a73d1c8c-2fd2-4f19-aa41-2df022bcb241-spons&psc=1&spLa=ZW5jcnlwdGVkUXVhbGlmaWVyPUFCS0c4UllTV09GTFImZW5jcnlwdGVkSWQ9QTA4NDUwMjlESzNKWDBHN0JBTEUmZW5jcnlwdGVkQWRJZD1BMDkwMTM0OTJPODdJREFRVU9RSUsmd2lkZ2V0TmFtZT1zcF9waG9uZV9zZWFyY2hfdGhlbWF0aWMmYWN0aW9uPWNsaWNrUmVkaXJlY3QmZG9Ob3RMb2dDbGljaz10cnVl https://www.amazon.com/Professional-Chassis-Platform-Accessory-Raspberry/dp/B08YFG42QH/ref=mp_s_a_1_37?crid=2O8QTTODWN37K&keywords=tank+arduino+kit&qid=1681967579&sprefix=tank+arduino+kit%2Caps%2C92&sr=8-37 https://www.amazon.com/Processional-Raspberry-Microbit-Avoiding-Obstacle/dp/B09KL2DP68/ref=mp_s_a_1_41?crid=2O8QTTODWN37K&keywords=tank+arduino+kit&qid=1681967579&sprefix=tank+arduino+kit%2Caps%2C92&sr=8-41 https://www.amazon.com/Professional-Absorption-Suspension-Supporting-Raspberry/dp/B09KLH5SKX/ref=mp_s_a_1_42?crid=2O8QTTODWN37K&keywords=tank+arduino+kit&qid=1681967579&sprefix=tank+arduino+kit%2Caps%2C92&sr=8-42&ufe=app_do%3Aamzn1.fos.006c50ae-5d4c-4777-9bc0-4513d670b6bc Hear are stand alone track kits https://www.amazon.com/SZDoit-Plastic-Chassis-Arduino-Learning/dp/B08J3ZSVGM/ref=mp_s_a_1_10_sspa?crid=4WGBPFJWLADR&keywords=arduino+tank+kit&qid=1681967788&sprefix=arduino+tank+kit%2Caps%2C86&sr=8-10-spons&psc=1&spLa=ZW5jcnlwdGVkUXVhbGlmaWVyPUEyM1BWRUQ5VlFYVE9PJmVuY3J5cHRlZElkPUEwNTU0NjY0VzlNSDBaVTE1UDhJJmVuY3J5cHRlZEFkSWQ9QTA5MDE3NDkxSUNQT1RWMjJIQk9IJndpZGdldE5hbWU9c3BfcGhvbmVfc2VhcmNoX210ZiZhY3Rpb249Y2xpY2tSZWRpcmVjdCZkb05vdExvZ0NsaWNrPXRydWU=
jstarne1 USA #7 Apr 2023 Oh the antenna dudes are magnetic arms to hold wires while soldering, the yellow base is a iron plate making some room for a servo, TaDa!
Oh the antenna dudes are magnetic arms to hold wires while soldering, the yellow base is a iron plate making some room for a servo, TaDa!
jstarne1 USA #8 Apr 2023 I’m sketching out the next part to 3D print, a servo to EZ bit camera adapter
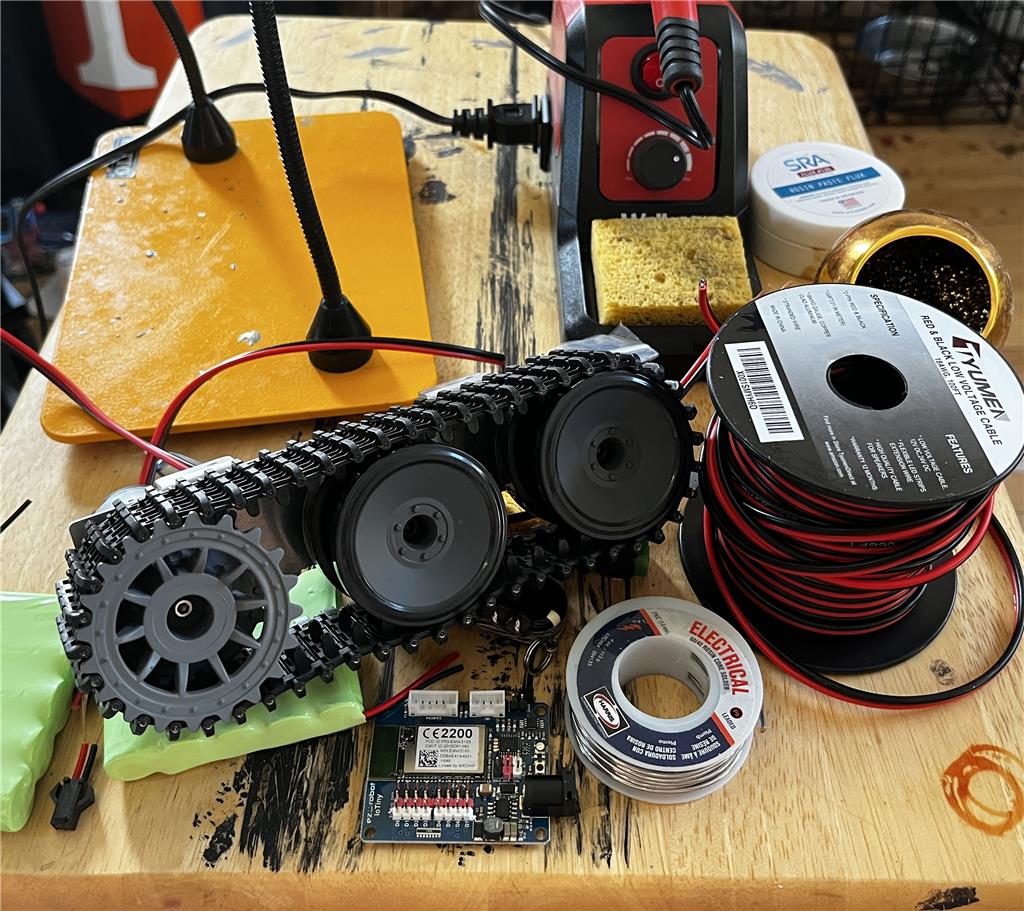
An IOT EZ Board in here..Oh this will be fun! I like guessing games
I soldered on long pigtails and a charging port for this 6v usb charger. No need to use a large specialized charger on this little robot.
6-12v spur gear motors get their pig tails and heat shrink. I am surprised at how quietly they run. Spur gears are known to make a wining whizzing noise.
I keep seeing those antenna-looking things in the back on the piece of wood.
Oh, and where did you get those tracks from? they look heavy-duty and real modular
This is a track kit from Amazon.com
https://www.amazon.com/gp/aw/d/B094N8DHVR?psc=1&ref=ppx_pop_mob_b_asin_title
https://www.amazon.com/SZDoit-Chassis-Stainless-Platform-Raspberry/dp/B07F41G9Z6/ref=sxin_22_pa_sp_phone_search_thematic_sspa?content-id=amzn1.sym.1ad53d03-de9d-4733-8030-19769ee35352%3Aamzn1.sym.1ad53d03-de9d-4733-8030-19769ee35352&crid=2O8QTTODWN37K&cv_ct_cx=tank+arduino+kit&keywords=tank+arduino+kit&pd_rd_i=B07F41G9Z6&pd_rd_r=ce7e3af1-729d-4f1c-a840-bd1370df12c0&pd_rd_w=yFpR7&pd_rd_wg=9ZcfV&pf_rd_p=1ad53d03-de9d-4733-8030-19769ee35352&pf_rd_r=J3CTBT24AM1DDMVKM9P6&qid=1681967451&sbo=RZvfv%2F%2FHxDF%2BO5021pAnSA%3D%3D&sprefix=tank+arduino+kit%2Caps%2C92&sr=1-3-a73d1c8c-2fd2-4f19-aa41-2df022bcb241-spons&psc=1&spLa=ZW5jcnlwdGVkUXVhbGlmaWVyPUFCS0c4UllTV09GTFImZW5jcnlwdGVkSWQ9QTA4NDUwMjlESzNKWDBHN0JBTEUmZW5jcnlwdGVkQWRJZD1BMDkwMTM0OTJPODdJREFRVU9RSUsmd2lkZ2V0TmFtZT1zcF9waG9uZV9zZWFyY2hfdGhlbWF0aWMmYWN0aW9uPWNsaWNrUmVkaXJlY3QmZG9Ob3RMb2dDbGljaz10cnVl
https://www.amazon.com/Professional-Chassis-Platform-Accessory-Raspberry/dp/B08YFG42QH/ref=mp_s_a_1_37?crid=2O8QTTODWN37K&keywords=tank+arduino+kit&qid=1681967579&sprefix=tank+arduino+kit%2Caps%2C92&sr=8-37
https://www.amazon.com/Processional-Raspberry-Microbit-Avoiding-Obstacle/dp/B09KL2DP68/ref=mp_s_a_1_41?crid=2O8QTTODWN37K&keywords=tank+arduino+kit&qid=1681967579&sprefix=tank+arduino+kit%2Caps%2C92&sr=8-41
https://www.amazon.com/Professional-Absorption-Suspension-Supporting-Raspberry/dp/B09KLH5SKX/ref=mp_s_a_1_42?crid=2O8QTTODWN37K&keywords=tank+arduino+kit&qid=1681967579&sprefix=tank+arduino+kit%2Caps%2C92&sr=8-42&ufe=app_do%3Aamzn1.fos.006c50ae-5d4c-4777-9bc0-4513d670b6bc
Hear are stand alone track kits
https://www.amazon.com/SZDoit-Plastic-Chassis-Arduino-Learning/dp/B08J3ZSVGM/ref=mp_s_a_1_10_sspa?crid=4WGBPFJWLADR&keywords=arduino+tank+kit&qid=1681967788&sprefix=arduino+tank+kit%2Caps%2C86&sr=8-10-spons&psc=1&spLa=ZW5jcnlwdGVkUXVhbGlmaWVyPUEyM1BWRUQ5VlFYVE9PJmVuY3J5cHRlZElkPUEwNTU0NjY0VzlNSDBaVTE1UDhJJmVuY3J5cHRlZEFkSWQ9QTA5MDE3NDkxSUNQT1RWMjJIQk9IJndpZGdldE5hbWU9c3BfcGhvbmVfc2VhcmNoX210ZiZhY3Rpb249Y2xpY2tSZWRpcmVjdCZkb05vdExvZ0NsaWNrPXRydWU=
Oh the antenna dudes are magnetic arms to hold wires while soldering, the yellow base is a iron plate
making some room for a servo, TaDa!
I’m sketching out the next part to 3D print, a servo to EZ bit camera adapter