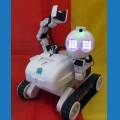
Stiko
Germany
Asked
— Edited
Hi @all. I have a little problem.
I use the servospeeds reduced. But when i activate my robot, comes the calibrate. The speed is so high that the components break. The construction is not very stable at this point.
I have try limit the speed with the command servospeed , before the calibrate starts. The servo runs uncontrolled in all ways.
After the calibrate, it works normaly and speedlimit.
What can i do for a slowly calibrate at first time after activate my robot?
Has EZ this white parts on the servos for a 3D print and where i can print this parts near my country?
At the moment i repair this with a strong glue.
Thanks
That is the speed of the servos - we have never experienced a break in the very strong plastic like this before. Superglue will not hold, you may replace worn parts. I recommend purchasing numerous replacement levers to suit your application.
*Note: please specify valid tags, not excessively. This topic does not involve 3D Printing or General. Thanks!
That's why I ask. Can I replace the printed parts only? But I do not want to buy a complete servo.
Shipping from abroad is very expensive. I have paid today again again almost 40 euro fee. For a package in the Vert for 40 Euro + 16 Euro shipping.
Can I buy the white 3d printed parts individually? Can I print these parts in Europe? (Shapeway)
I can not believe this is the first time. I already have a broken contact at the servo and A broken extension cube.
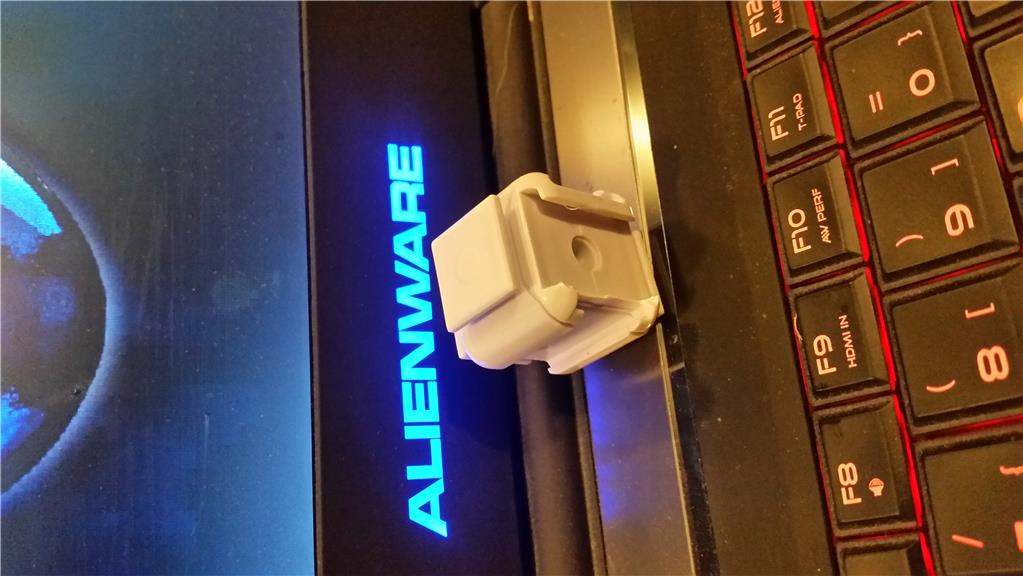
The question relates to the 3D printed parts of EZ and Their files. This statement I do not understand.There is no 3d printing parts sold on ez-robot.com. You may 3d print your own parts or ask someone to print them.
EZ-Robot only sells injection molded plastic parts. You certainly can get ez-robot injection plastics without servo. Use the Contact Us and request to purchase plastics.
When a servo initializes into position, it does not know what position it was in before. A servo only knows the position it is told to be. So when a servo is initialized, it cannot move slowly to a new position because it had no idea what position it was in. A servo responds to position requests, it does not know positions.
Find out more how a servo works here: https://synthiam.com/Tutorials/Lesson/48?courseId=6
hi stiko
i can send you a bracket in a letter.will cost you nothing. if you have an adres for me. one question for you ,when you connect jd does he trow his arms all the way back - warts ?
you can contact me on skype patrick.dierckx19 or
[email protected]
Thanks @DJ for clarifying this misunderstanding.
I thought everything is 3D printed. Download CMD file, go to Munich and print. I thought that was too easy.
@Nomad 6R, many thanks for the friendly offer. This is really very nice of you. I will be glad to contact you.
I use JD on a rover. The arms were extended by 2 servos.
The project and the servos work perfectly. All functions are normal.
Because of the connection to the Rover, I can not lay the body flat on the floor. When I start the robot, all of the servos go to 90 ° quickly. This is so fast that the innermost parts are extremely stressed. The length and weight of the arms provide a strong load at this moment. It is the strongest load my robot ever gets.
I will have to experiment with a different start position.
stiko
is it possible you put the bracket when calibrating in the wrong position ?
it looks like the servo D4 is trying to go to position 90 degrees. but got stuck against the chest.you can see the broken part on the chest, has shiffted backwarts.means the servo still trying to reach 90degrees. many made this mistake including myself.
I have an extra long arm on my Roli, similar to what you do, and I could see that when they snap to the initialization position it could cause some strain. I have mine initialize with the arm pointed straight up, so the joints aren't carrying a lot of weight, and then I re-position at a slower speed into a "resting" position that lays the claw on the body to take up some of the weight.
I also try to get into a position near the initialization position before shutting down if I can get to it before the EZ-B stops responding when I get the low battery alert (I could probably script something if I really wanted to, but I have never had one of the brackets break, so didn't think it was that big a deal, just being cautious).
Regarding your questions about 3D printing. The STL files of all parts except the ROLI body are available, so you could go to a 3D printer to have replacement parts made, but in general, I think the injection molded parts are going to be stronger than any 3D printed part, so better to get replacements from EZ-R through the "contact us" link (and very nice of Nomad to offer to send you a spare).
Alan
thanks alan
its allreddy in the mail.bracket+cube
happy christmas averyone