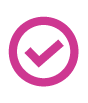
I'm running a 12 volt 3 amp power supply. Then I have a 12 volt to 6 volt DC step-down to power my EZ-B4 and servos. After the robot runs a little while sometimes the servos stop responding. But most often If I run a script to put the robots arm on its hip, sometimes it will work. Other times the arms will start to move and then the EZ-B4 will disconnect and then reboot.
I have also seen that after running a while the servos in the arms will start to run slow and not quite make it to there assigned spot. While the servos in the neck keep right on going like normal.
So I was thinking we did not have enough AMPS for all the servos. See I have 2 servos in each shoulder, one servo in the elbow, two servos in the wrist and one in the hand for a total of 6 servos in each arm. + 2 servos in the neck.
Test 1 I started to look at the power supply. Maybe we do not have enough AMPS. So I grabbed one of R2D2's 12 volt 18 amp hour battery. R2 was not vary amused to see one of his battery's wandering off. While the servos ran a tad bit faster I soon ran into the same problems.
Any ideas? confused
see below 7.4 volt and 4.5 amp
servo
@Slee The Sloth.
It does indeed sound like the power supply you are using is not supplying enough amps for the servo inrush. That would be the main cause to why the EZ-B is resetting. 3 amps will defiantly not be enough for servos. The current advice that other users and myself mention is to use a supply that can produce at least 15 or 20 amps, minimum, if using a plug in power supply. The other options are Lipo and Nimh battery packs which can handle the current output.
Another thing to keep in mind when using a step down converter or regulators, as well as output voltage, is the amp output too. You could be suppling 12 volts and 20 amp input supply through a 6 volt regulator for example, but if that regulator is rated for 3 amps output, that's all your servos will get... 3 amps. So you would need a buck converter or regulator that matches you voltage needs, but with a much higher current output.
Hope that helps.
This makes me kind of wonder, why this happened on the 12 volt 18 amp hour battery just the same as the 12 volt 3 amp power supply. I run my full scale R2 off this bugger ( 12 volt 18 apm hour battery) and he has 13 servos + 2 drive motors and then servos and Arduino's.
I do know how to test this though. I will use 2 of my 12 volt 18 amp batteries and see what happens.
You have 12V servos or are you using a voltage regulator to drop down the voltage to 6/7.4V for the servos? Your step down can't provide enough current for the servos to run even though you have a huge 12V SLA battery as your power source.... You will need 20amps+ at 6/7.4v not 3amps to handle the "inrush" power requirements of multiple servos... Your step down regulator is your bottle neck....
What is your step down converter you're running the servos/v4 off rated at for current/amp output?
he wrights 6 volts
@nomad.
Voltage is not the problem or the question here. It's amperage/current.
@nomad... 6V or 7.4V it doesn't matter... his voltage converter is not able to supply enough current to move multiple servos....
@Slee The Sloth I just bought 20 of these for the exact purpose of what you are trying to do ... Variable volatge regulators You would use 1 (inline) per servo....
P.S. Steve figured out your problem so you should give him the credit for resolving this...