
PRO
afcorson
Australia
Asked
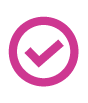
The dreaded jumping servo problem has arisen again - just today. All servos in the robot are HDD. The servo on port D0 now jumps after connecting, to about 35 degrees instead of 90 degrees. If I move the servo manually when turned off, the centre position is still 90 degrees, so the sprocket has not shifted. My INIT script has not changed. That servo is set to 90 degrees. Has anyone had this problem before? I am thinking I might have to replace the servo and see what happens. My previous problems with jumping servos were because I had a HD servo. But not this time.
Related Hardware EZ-B v4
As far as i recall when I used to be part of EZ-Robot, the HDD servos were impossible to jump. As they were designed that way to remove the jump. Perhaps they're jumping if the wire is loose on the connector into the ezb? That's about as much as I can suggest as Synthiam is not part of EZ-Robot.
You can reach EZ-Robot, who makes the servos in question at www.ez-robot.com and they'll be able to answer more questions for ya.
Just to narrow things down and pinpoint where the issue really is try moving the servo cable attached to D0 to a different pin. Ideally swap it out with a known working servo with no jumping issue. If the issue stays with the servo after attaching to the new pin then the problem is the servo or with it's wiring or connectors. If the known working servos suddenly jump when turned on when attached to D0 then it's in the EZB or your script.
ever have those days where it's, that servo is blown, ill guess i will try another one, wow that one is blown as well! It is not until after the 3rd one blows you realize were putting 16v into 5v servo's and blew them all up.
Nink oh no!!!! Now that’s one of those days for sure
Replaced the servo and that fixed it. I hope this doesn't happen too often as it took an hour's work to replace. Also damage can occur when servos jump around. I was lucky this time.
Have you contacted ezrobot about their servos doing that? We unfortunately can’t help you with hardware issues like that. Synthiam doesn’t make any hardware. But it’s great you sorted it out - however they’d like to know about their servos I think
i have an HDD too that does this . i removed any lines that included this - stop() it looks when you connect to your ARC a second later . its rather violent .
If you have HDD servos that jump when power is applied (not position being sent) then contact the manufacturer. The manufacturer is ezrobot. Synthiam does not make servos or any robot hardware. The website is www.ez-robot.com
Synthiam does not have the resources to support third party products. Contact the manufacturer please.