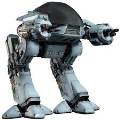
Aceboss
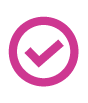
I was running JD successfully last night, up until the time I had to put him on charge. Charged up the battery, disconnected after the charge. Tonight after powering him up as usual, I found one of the servo's (Port D5, his left 'forearm') was unresponsive.
Symptoms are: the servo doesn't move when instructed. The servo is able to be rotated by hand even when it should be 'locked' in place (similar to it's powered down state in battery saver mode). There's no change if I place him in the 'calibrate' position. All other servo's are in their normal calibrated position.
There was no smoke and no buzzing from the servo last night prior to powering JD down. I have disconnected the servo from the port and reconnected it as well. There are no obvious signs of the wires at either end being frayed or unusual.
I am wondering if there's anything else I can try, or if this is an indication of a dead servo? I received JD just over 2 weeks ago.
Any advice would be appreciated. Thanks.
Try the servo on a different port - instead of running the JD project, just start a new project and add a single servo control. Define it for the port you are plugged into and set the minimum and maximum values. If the servo is working it should move as you change the values.
Servos are wear items and can burn out, particularly if they try to move beyond a physical limit or otherwise have their movement hampered (cable pulled too tight... A common mistake is threading the servo cable through the rectangular hole in the end of the lever. That will cause the servo to bind and burn out).
I had one EZ-B digital port fail, but it was completely my fault and would not occur with a servo plugged in (shorted out the pins).
Alan
Thanks Alan,
Good suggestions, unfortunately no luck. Changed it to Port D23, opened a new project as suggested, added a horizontal servo control, tied that to port 23 and set min to 45 and max to 113. No movment at all when running the control through the allowed values.
I can see what you'd mean by threading the servo lead through the rectangular hole, but that's not the case here either.
JD occasionally emits a low hum when coming to rest between autopositions, but I believe that's normal, he certainly never emitted a loud buzzing, and each servo had gone through both tuning, and then fine-tuning originally with no adjustment values > 10. There's no visual discoloration on the outside of the casing to indicate a burn-out either (I'm not techy enough with hardware to feel confident of checking the inside of the servo casing).
Any other thoughts or do I need contact the robot hospital and order another servo do you think?
Edit for clarity: There really is no such place as robot hospital, it's just what I tell JD to make him feel better.
Unfortunately it sounds like you need a new servo. It is possible that it is just a loose connection inside, but if you aren't confident with checking inside the housing, then it may not be worth it (although if you are going to be doing a lot with robotics, getting handy with a soldering iron would not be a bad skill to learn).
You could try clicking the Contact Us link and reporting as a warranty issue (reference this thread). I am not sure how EZ-Robot is handling warranty issues on servos these days since it is so hard to determine if there was abuse, but since yours is only a couple weeks old, they may take pity on you.
If you do need to order, I would get several spares since the shipping costs for just one servo are more than the servo itself costs, and because they do occasionally burn out. Robots like JD and Six, where all of their weight is held up by the servo's active location holding are more likely to burn out than a Roli or Adventurebot too. I would not expect to lose a lot of them. I have had Revolution robots since they first started shipping and only had one servo burnout and it was completely my fault (claw too tight for too long when I got distracted), but I still have several spares just in case.
Alan
Roughly 2 weeks ago, I got a JD too. After the excitement of watching JD several dances (several charges, quite continuously during a day) upon finished building, both shoulders "died", one freely moved but no response, and the other locked up but didn't moved nor responded, and ended the cheers and happiness of all the watchers old and young.
Also I got a Six a month ago, until now 2 servos died too.
Upon opening the servos, I can see that one of the FET, if not both, on the little circuit board have the usual sign of burnt-out, and smelt. (Wonder if ezrobot has any replacement of this little circuit board for the servo?)
Thx Alan, I'll contact support but also order some spares as you suggest at the same time, since shipping is (as you say) relatively costly.
@DJ
Have you recently examined the currently shipping servos to make sure your manufacturer is accurately following the BOM? If you recall this thread from Giskard https://synthiam.com/Community/Questions/9282 she was trying to point out that it looked like the servos were using cheap knockoff Mosfets rather than a branded Mosfet 9926a (I think you missed that point and went on to explain what a Mosfet was, which she obviously knew).
If that is what you are paying for, and you are satisfied with the performance, that is fine, but if you are paying for 9926a's and not getting them, it might explain the slight uptick in forum complaints of early servo burnouts over the past couple of months.
Alan
The servos are great still - only people with an issue will post on the forum. So, the one user per month with issues is pretty good
also, if you look at giskard's custom builds. There are some questionable builds with incredibly long arms being lifted by a single servo - which disregards all servo warnings and usage.
Servos are a wear and tear item - and will damage over time. Specifically when used in a robot that is carrying a significant weight.
You can revisit that thread to read my reply regarding that you cross-your-fingers that the mosfet burns out rather than a fire. Be happy the mosfet is damaged instead of the wires catching on fire, the battery exploding or worse...