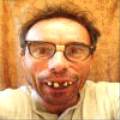
PRO
Herr Ball
USA
Asked
— Edited
Hey all
I am attempting to hook up my Sabertooth 2x25 but am a little confused here. Have read two different places here how to connect?
https://synthiam.com/Tutorials/Help.aspx?id=173
Says to hookup as "Simplified Serial Mode at 38400 baud rate"
While
https://synthiam.com/Tutorials/Hardware.aspx?id=26
Says "EZ-Robot suggests connect Sabertooth Motor Controllers in R/C mode. This allows the user to control the motor speed and direction with the Modified servo Movement Panel. "
I believe that the second link is what is needed as speed control is a must. I don't want to use a joystick just the EZ-board. Any thoughts here?
Herr
The instructions to use serial mode are more recent, and DJ posted answers as recently as 2/28 with that instruction. I haven't hooked mine up yet, so I am only able to comment on what I have read here. Searching for Sabertooth gives lots of interesting posts.
Alan
Thanks for the reply
I have been messing with it for most of the night and can't figure a way to get speed control using the serial mode. It's getting late here, 1:30 am lol, so tomorrow is another day. Maybe I'll crack it in my sleep ... lol
Herr
Speed control is going to be important to me too. Hopefully someone else will chime in here with advise. I know @rgordon has had success with his 2x25.
Alan
I just read the 2x25 manual from the dimension engineering site. It is a little slim on details, but if I am reading it correctly, packetized serial allows speed control, but simplified serial is either full on or full off, but nothing in between. It looks like if we need speed control, connecting it in R/C mode and using the modified servo panel rather than connecting it in serial mode with the H-bridge panel is the way to go.
edit... I may have mis-read. It may support speed control, it just isn't as clear as it is with packetized serial. They give values for full reverse, stop, and full on, but don't say one way or another for values between them. They could be speed values.
Still hoping DJ or someone else can confirm.
Alan
Well I messed with the numbers in the modified servo control trying to get it up and running but was never able to make it work correctly. One time the motor would go forward and one time it would go backwards, never could zero it in!
Hopefully someone that has gotten it to work will see this and clear up some things.
Herr
I used two Sabertooth 2x12 controllers for my ARMadeus project, one in RC mode the other in simplified serial mode, to control 4 linear actuators. I used the right joystick of my game controller to operate 2 of the linear actuators, allowing both speed and direction control. The other two actuators were controlled in the serial mode by using game pad buttons. A SendSerial command string was assigned to each button press, using 4 buttons total. Any speed and direction can be assigned to the button by sending the appropriate byte value. I hope this helps.
Jim
Thanks Jim for the reply.
I hope some others can be helped out from your post but for me I'm not wanting to use any joystick or game pad. I'm sure there is a way to do this but just can't find it.
Herr
@Herr Ball,
I'm using the HBridge/Sabertooth Serial Movement Panel. A screen shot of its config is attached. These values as far as left/right and fwd/rev could be different on your Sabertooth controller depending on how you connected the motor wires.
Left Motor = 1 to 127 (Full Rev = 1, Stop = 64, Full Fwd = 127) Right Motor = 128 to 255 (Full Rev = 128, Stop = 192, Full Fwd = 255)
Sabertooth Dip Switches, 1, 3 & 6 set ON (Mode 3, 38,400 Baud Simple Serial) EZ-B D8 signal wire to Sabertooth S1 input
Also see this thread about how I get it to switch between EZ-B control and R/C control
Dip Switch Configurator Circuit