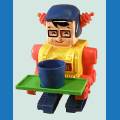
Mulberry
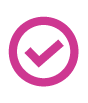
Its Sunday so I must be having H-Bridge problems
So I'm attempting to set up another Pololu H-bridge on a second board. I currently having one working smoothly so I copied the configuration and settings however I've been unable to get any motor activity. I was hoping someone could take a look and see any glaring mistakes.
Power
Power to Polulu from 12 volt source (same type of source I've used on another H-bridge set-up). Power to EZ from 12 volt source. Motor is 24 volts but I'm running it at 12 Common ground between Pololu power connection and EZ power connection
Connections
Full cable connection (white, red, black) to DO Port 1st Signal connection to D1 2nd Signal connection to D2
Port settings in EZ are
Left Trigger A DO
Left Trigger B D1
Right Trigger A D2
Right Trigger B DO
PWM set at:
Board 3 (correct board) Port DO
Sliders all the way up (on)
I read power entering the Pololu board and power leaving the board and entering the EZ.
Can anyone see a problem here? I have tested this configuration with another H-bridge and another motor.
Again I have another H-bridge running smoothly on another board with the same configurations.
Thanks,
- Scott
Not knowing your set up but from what you have discribed, this might explain the problem.
If you are using two or more v4 boards on one ARC project, a movement control panel controlling a H-Bridge will only work with the first board, mainly board 0. For example, if you have a H-Bridge connected to board 0 and using a movement control panel, connecting another H-Bridge to board 3 won't work. It would have to be connected and controlled by board 0 as well (although you can only have one movement control panel per project, but multiple H-Bridges can be used).
Is thet similar to what you are doing?
H-Bridge movement control panel tutorial
Thanks Steve
These are separate projects and unrelated. Each of my controls (waist movement, head rotation, and other components) exist as a separate project with their own dedicated EZ board. So one H-bridge per board. I open a project to control a movement. My plan was to go this route until I was proficient at script.
Are you saying I can't have multiple projects open if I want to use this route to control more than one motor movement?
D Scott
No worries. In answer to your question, I've never tried it. With multiple instances of ARC open, I think that each individual project, with its own v4 connected to it, should control their own movement panels fine.
Why are you using board 3 in the project related to this post? With a different board on its own project, you can scan to find the board, and use board 0. I'd give that try to see if it helps.
That does work but when I use 0 on each board for each of my H-bridge movements then I have to shut down each board before using another one. The signal goes to whatever H-bridge is active. I think I misinterpreted the 0-4 range . I thought they designated separate EZ's s and I could add an H-bridge to operate independently. I use 0 for waist rotation, 2 for head rotation, and so on.
As far as I know, the zero to four range is for connecting multiple boards to one project.
Depending on if you have enough available ports left, you could connect the second H-Bridge to board zero or board 3 and use simple scripts to control movement. This could be using separate script controls, or for example, use the mobile interface to create your own buttons to control each H-Bridge for each portion of the body.
Since you are using h-bridges for what it seems as simple left/right movements and such, can't you use basic scripts to do the same? This way you get around the one Movement Panel restriction....
@Mulberry.
That what I was planning on doing on something a while back, not using movement control panels, and just script the simple movements using the digital ports for on/off and PWM. If you use board 3, just remember to add the 3. in front of the port number in your scripts, for example Set(3.D1,On)
I think Daniel is a little worried about having to write scripts. This seems to be the reason why he's useing several ARC programs opened at one time to be able to use more than one movement panel.