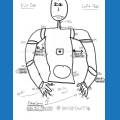
Dunning-Kruger
Canada
Asked
— Edited
Hey Tony, Just got those Bosch servos... thank you so much... Can I ask one more favour? What are the pin outs on these?... There appears to be 5 pins with a recessed sixth... I assume 2 are for a 12V battery and the others are used to drive the motor... Just don't know which one is which...
Thanks Richard
@Richard R
Open it. The 2 powers the motor and the 3 pins go to the pot
@DoomBot... my electronic knowledge is not as polished as yours Marc LOL.... I did open it... So the 2 lower pins go to 12V and the 3 upper pins plug into the ezb for control? That doesn't sound right.... Can you confirm?
Ok, I think I get it. It needs some kind of H-bridge motor controller... I managed to read the pot... Before I hook up a motor controller to the motors... Is this thing 360 deg rotation or is there a physical stop like a regular servo? I am thinking it is something like max 250deg rotation or so?
As far as I know it's 360 but you can use scripting to read the ADC pot and call your positions like that... the wiper is the middle pin of the pot so it goes V+, Signal, Ground. As far as the 2 pins yes you need an hbridge to get PWM and direction
Richard R, I had this saved for bosch, but the spec page will not display. This is the closest I can find till Tony responds. Post 276
https://synthiam.com/Community/Questions/2263&page=28
Steve S
@Doombot... I have been rotating the motor worm gear by hand... Slow process LOL... Stops at 225 - 230 ... So these must be limited rotation since the pot can only read to a certain value... Looks like 1 - 225 degrees...
@Steve S Thanks, I will have a look....
Richard R, I think the pot only controls 100 degrees. Steve S
I was able to read 1 to 225 slowly cranking the motor by hand... Either way I get how they work now... I need a servo or motor control board with them.....