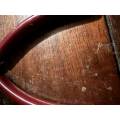
Redzone
USA
Asked
— Edited
Hi Richard I've seen on some posts that you recently have an encoder you had given me a link to the motors and wheels that I currently have now on my inmoov could you send me a link of your wheels and encoders that you currently have thanks
@Merne... Are you sure that was me? I have yet to use encoders with anything.... I do plan to get my kangaroos working with my sabertooth at some point down the road, however....
@RichardR, well I thought you had the encoders I thought it was on the post that do you D.cochran had put out there.
any case do you plan on getting encoders or a whole set motor with wheels and encoder I ask you only because the wheels and motor I got the link from you last time I like them same ones Bob Houston is using as well
Thanks
Hi Richard R,
Didn't you talk about some motors with a plastic case and some kind of disk? The disk moved and got chewed up or something like that? Or was that Dave? I think the original conversation was about platforms available. I trashed all my old notes so I am not sure of the details. I knew I should never clean my desk!
Ron R
Wasn't me... that I recall anyway....?
It wasn't me offering a solution to anything I don't think, but memory isn't what it used to be so it is possible that this has slipped away from my memory.
There are many types of encoders along with many ways to use them. There are many considerations on which encoder is right for what you want to do along with environmental conditions.
If an encoder were placed close to the wheel and were not protected, simple things like carpet fibers and dirt could obstruct the view of the optic. Magnetic is an option here, but a metal sliver could then still do the same I suppose.
I found that an encoder placed at the back end of the motor that was enclosed and protected from light or dirt was the best solution. This allows for a very high encoder count per wheel revolution. Sometimes this was too high but a solution has been found, tested and is being built to handle this issue. The motor does require a back shaft that the encoder can be mounted to. This is how industrial encoders normally work in order to improve reliability. I will say that DigiKey has a huge selection of encoders. They are not always available, but it is a good place to start your search.
A friend of mine has 144 count per wheel revolution encoders. He doesn't feel that these are high enough count encoders at slow movement speeds. If these encoders were before the gearing I would suspect that they would be more than enough for what he wants to do. I suspect that they are after the gearing though which is why there is the low count per rev.
I did a lot of research and asked some questions off line before I chose the motors that I use. @Toymaker recommended the motors that I use and after doing even more research, I came to the conclusion that he was spot on with his recommendation. These motors are expensive at first, but when you look at what you are getting for the price, they really are cheap.
If you try to buy this motor... Globe IM-15 E2435 445A117
You should find that these are on sale for about $200.00 each without the encoders. These are industrial grade fully enclosed motors that handle up to 300 oz/inch continuous torque or 18.75 lb/inch continuous torque per wheel. The size of the wheel then comes into play and the weight distribution to a third caster style wheel and the friction that wheel has along with some other variables.
There are many different types of encoders for these motors at different counts per rev. I use a 500 count per rev encoder because it is what came with the motor. I had done some research to understand what the labels on the encoders meant and here is a quote from that post with a bit of cleanup.
These encoders cost about $40 each and are fully enclosed and rated for use in industrial environment. They are really good encoders but this brings the cost per motor up to $240.00 per motor. This is pretty cost prohibitive for people and are meant more for industry in the first place, so this cost is more suited to that type of customer.
Luckily, http://www.zagrosrobotics.com/shop/item.aspx?itemid=639 has these motors with the encoders for $129.99 each. They are the exact same motor and the same encoder, but because of the encoder counts per revolution (500) and the gearing to give the torque (127.27:1) you get too many counts per revolution for most consumer grade components. $129.99 per motor may seem high, but you are really getting a motor that is absolutely setup for industry conditions and that carries with it a price tag. Is it overkill, possibly, but I think it is overkill in a great place personally.
The issue with too many counts per revolution has driven some away from this motor. There have been solutions hanging out on the boards for months, but these were only recently tested and proven to work. For documentation sake, here is a link to a lengthy thread with the final results of these tests included. https://synthiam.com/Community/Questions/6225&page=3 This page also shows the wiring for a specific chip which was tested and proven to work. This solution would cost you probably $20 per motor to breadboard (including the bread board and wires), of which about $10.00 would be shipping.
If you took the cost of the motor from Zagros and added $20.00, you will see that you are really getting one heck of a deal from them compared to trying to purchase this from someone else.
Most of the weight of the robot comes in the form of batteries. Most large robots use Lead Acid batteries which are very heavy and really handle very few charges, but at first glance are very cheap. I recommend looking into LiFePO4 batteries that CONTAIN BALANCE CIRCUITS. These are meant to replace Lead Acid batteries. I would also make sure that the ones you look at can be run in parallel and serial type configurations. Not all of them are made to do this. These batteries cost about $280 each. That seems like a really high price tag, but let me explain why it isn't at all.
Excluding the weight argument for a bit, these batteries can handle on the low end 1500 charges. The Lead Acid battery can handle about 500 charges. If we took the cost of the LiFePO4 battery and divide by 3, you get $93.34. This is more reasonable for sure. Now, if you were to take how long a LiFePO4 battery lasts per charge and compare it to a lead acid battery, on the very low side, you are going to get about 4 times the run-time per charge. This is from real world testing that I have done. If you take this and calculate it in with the refactored cost from above of $93.34, you will get the real comparison cost of $23.33. This isn't calculating the weight issue (which is what I was trying to get to in the first place), oh and on demand amps.
LiFePO4 batteries can deliver 1.5 to 2 C of on demand amps on the low end. For a 20 AH battery, that is 30 to 40 on demand amps. This is more than sufficient when compared to Lead Acid batteries.
Now to the weight factor.... The LiFePO4 battery weighs in at about 1/2 of the lead acid battery due to its usable capacity in relation to the installed capacity.
So, for cheaper over time, you can get a battery that weighs half the weight and performs better than what is perceived as a cost effective battery. Again, you have to use the ones that have the built in protection circuits if you want to use normal car chargers with these, but it is well worth the added cost I believe and will allow your robot build to decrease in weight drastically, while providing a longer run time, and far more charge cycles.
This was a lot of rambling, but I tried to cover everything pertaining to the motors which are directly related to weight, which is related to batteries.
@Merne, feel free to call me if you have any questions about this.
@Richard R
The post Andy is talking about is where you mentioned the Arlo base.
synthiam.com/Community/Questions/6225
@rgordon Well there you go a year ago LOL.... So yes, I never got to actually use that encoder because it broke before I had a chance to.... For a future project, however I am going to go the route of buying motors with encoders on the back (like the ones David mentioned) and using a kangaroo/sabertooth combo....
@D.Cocharn, thanks David the information will help a lot it will take me a couple days to fully understand it but that's just my brain LOL
I think I will go with the encoder motor that you had put on here ,would you know how much weight they can handle my set up with the SLA batteries is about 75 pounds do you think it will handle this set up. Thanks.
@richardR lol I looked at that link and it was a year ago . I can't remember what I had for breakfast yesterday.
Thanks everyone else for jarring Richards memory