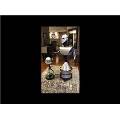
Ellis
Has anyone thought about the next step in Ez-Robot offerings?
I am so impressed with what ARC has done with the existing EZ-Robot. You can not find anything like it out there. I have always used the DIY kit to build all my robots.
I am now wanting to start building a more robust semi commercial robot that I could eventually build and sell. It would need steppers for more accuracy and digital response than the existing servo's cannot supply. It would need a more robust communications offering to give it wider bandwidth and coverage.
I love the existing software but it would need to be upgraded to take advantage of the stepper motors and communication upgrade. The format is already there. It seems it would not be a great step to take the existing software and adapt it to the new system.
I can't wait until EZ-Robot comes out with its new Ez-Robot stepper offerings and accessories.
I know it would cost more but I think most builders would be willing to pay the added cost for more robust and powerful robots that could become real house servants for example.
What do you think.
I don’t understand. What limitation do you think ARC has? There are no known limitations because it controls any hardware - because it’s an expandable platform. You can control stepper motors with ARC. Explain more and I’ll direct you, outside of me doing the actual work.
For example, what do you mean by...
steppers for accuracy (what are you comparing steppers to? Servos? How do you relate a stepper as having higher accuracy than a Servo?)
digital response (what does this mean?)
where did you hear that ezrobot would have a stepper product or offering? (Ezrobot has no interest in outdated stepper motor hardware. There’s an over abundance of legacy stepper motor hardware available from china left over from past decades, which are affordable for your experimentation.)
Perhaps this is a good opportunity to introduce new servo technology - such as used in darpa humanoid style and manufacturing robots. Dynamixel servos by Robotis are a good starting point - because their positioning system is top notch. There are chinese knockoffs with lower price point, as well.
The fact is, once you go down the path to manufacturing a product, you don’t use servos and parts from other companies - that costs too much.... which increases the product price and decreases revenue.
your manufacturing process would include your own servo mechanism. This can be influenced by Dynamixel tech, but not stepper motors - at least not alone.
If you decided that stepper motors are the right choice, then each motor (like a Servo) would have its own controller. This is the same as an hbridge for a motor. This controller consists of transistors to manage the high current necessary for a motor to operate from a micro controller signal. Find out more in the learn section of this website on how servos work.
I believe the start of this conversation is misdirected from ARC limitations, where it should be on education.
Everything ezrobot does is educative... because the platform is theoretically limitless - so our mandate is to educate users. Let’s start there... tell us what you’re wanting to do, and we’ll tell you how to do it.
@DJ can you tell me the name of the Dynamixel knock off? I’d like to do some testing on those!
this is the only one ezrobot natively supports with a plug-in: https://synthiam.com/redirect/legacy?table=plugin&id=171
Others will require google. Search for terms like serial Servo
Related to the original question, absolutely any peice of hardware you find on earth can be connected to ARC. You can do this by either string EZ-Script or make a plug-in. I highly recommend making plugins because they are portable and easily distributable.
First I want to say that I am in no means saying that ARC was lacking anything or could make their product any better. It is as far as I am concerned no one out there that comes close.
Sorry DJ if I didn't explain myself better or I really do not understand some things. Servo's as I understand have rheostats. Stepper motors have set pulses to be more accurate. See attached url https://www.lifewire.com/stepper-motor-vs-servo-motors-selecting-a-motor-818841. This article expresses what I am talking about.
When I say digital response and accuracy I am talking about using stepper motors since they have measured steps to calculate exact positions verses a rheostat which uses a measured voltage to calculate position. As far as I know when making 3D printers they use steppers as a go to motor because it is easier and more accurate.
I know that Ez-Robot can just about control everything but it sometimes takes many ports to accomplish this. What I was alluding to was using one port to control one stepper by just plugging it in similar to a servo. Then set up the stepper much like we do servo's now.
I understand Ez-Robot is an educational system. It is the best out there. I like it so much that I now want to make a more robust robot. Forget manufacturing anything. What I am talking about is making larger more powerful robot that can be accurate to two thousandths of an inch and lift 25 lbs. If we can go this with existing Ez-Robot system I am very much looking forward to doing that.
Once again thanks for all the help.
Ah - I see where you’re coming from with steppers. Don’t worry about the education part, just ask and we’re here to help
. When we say the limit to the platform is your imagination - I’m very serious, because that is your only limit. And I keep making sure the platform is limitless - doubly so with plugins! That part is super powerful.
So let’s get right to it!
Stripper motors are used in 3d printers because they’re both cheap and with appropriate gearing, provide a determined resolution. A stepper has a resolution but there’s no feedback. The resolution of any motor source can be altered with gearing, as you see on the belt of a printer. The stepper itself would need gearing / but the position is still unknown.
If you ever see a printer get stuck, it knocks off its alignment of assumed positioning until it’s cakibrated again.
The advantage to a stepper is for things like hard drives heads and light movements, unless gearing is used / but again, no feedback on position.
The reason servos don’t use steppers is because you get higher position and known position with feedback. This can be done with potentiometers OR counters. Both use analog but it’s converted to digital.
Higher quality servos, such as dynamical use counters. Wether magnetic or light wheels.
While you could theoretically use a stepper with positioning feedback increases price and redundant because the stepper when combined with feedback is redundant.
Oh - I should also add that stepper motors are not efficient and generate a lot of heat. Specifically in a stalled state "holding assumed position"
Lifting a lot of weight is best using a servo motor designed for the weight - such as a dynamixel servo. They have high torque versions, which are costly because they're used for prototyping/design r&d. Once your product gets designed for manufacturing (DFM), the cost of components is evaluated against redesigning in-house. For example, a dynamixel with high torque may cost $100 per unit - which is far too costly for a product component. The would make the BOM expensive and reduce profit and increase product MSRP.
To r&d a product, use dynamixel or servos that fit your requirements. Then, once a working prototype is established, explore lower cost options.
The easiest way to produce a geared feedback servo-like mechanism is with a motor, not a stepper. Then, evaluate how the feedback would be determined. This is actually quite easy and can be done in prototype with an arduino connected to EZ-B. There is arduino code that demonstrates servo-motor feedback.
Each servo-mechanism you build for joints would have their own low cost controller. Low cost ST Micro or Microchip microcontrollers will do the job, and cost under a dollar.
Implementing a communication protocol, or adopting an existing protocol is also quite simple. And gives you control over how the power and signals are distributed. This leads to the topic of addressable serial communication, which is the most popular with lowest overhead. Each controller has an address and only responds/transmits information with the address. This allows only all servo controllers to be connected in serial with the same wire (one for tx, one for rx).
An example of a feedback 3rd party servo-motor controller board is Kangaroo from Dimension Engineering. With that, combined with a motor controller, any motor can become a servo. Dave, on the forum who built the B9 does that, for example. He built his own gearing and feedback mechanism which uses this approach.
Many others have as well, including ToyMaker with his EZ:1 robot
So, in summary
prototype with 3rd party servo motors such as dynamixel
design your own gearing/feedback controller for cost savings and choose a feedback mechanism such as potentiometers or wheel/light encoders
build product
:)
Great info DJ.
Thanks DJ.
This clarifies several of my motor and control questions. Like I said I want to create a robot that can do really useful human things and know I need to do a lot of research.
This really helps. I presently have an EZB controller, which uses all the ports, and 12 Ez-Robot HD servo's running my existing robots arms. By the way I am calling him Tim Man. He will have adjustable height capability and be 36" to 60" in height. His body will be covered with aluminium sheet metal and will remind you of Wizard of Oz. All arms will have all human capability plus some.
I am sure I will take you up on help from the community to accomplish this.
Thanks
Ellis