
antguru
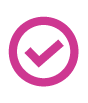
:D here is a thought that needs some pruning. I need a linear actuator that has about 10 inches of travel. 256 mm. A 15kg rc servo has enough torque but presents a control issue. I would like to get 1mm resolution. I was thinking about moding a rc servo for continuous rotation and adding a dual photo detector inputs and feed the inputs to the a/d ezb inputs. The detectors would be placed 90 degrees out of phase so the ezb could decode the quadrature and count the linear position. Now the real question. Should I use the servo feedback system somehow? Or should I do the math in the ezb and just alter the servo pwm signal somehow? All idea's are appreciated and if anyone has any scripts that might be used, please post. BTW the rc sites have no solutions that I can find, other than very expensive actuators. Thanks Neil
This is a repost since I received no feedback.
Do you have a 3d printer?
What are you thinking DJ I have access to a 3-D printer
I think DJ means that if you want that type of precision movement maybe hacked stepper motors and control board from a 3d printer might work...
What you want to do seems like a serious custom job...
Lol, I've done a linear actuator without feedback
I also only had about 3 inches of travel.
A 3D printed (or threaded rod) worm gear assembly is probably a good way to go, instead of encoders you could have end stop limit switches. This is the idea that most 3D printers use on their x and y axis'.
Some interesting feedback. If I switch to a small stepper design does anyone have a suggestion for a inexpensive pwm to stepper motor controller that the ezb digital servo output would drive over a total distance of 10 inches? or is there a better way of driving a small stepper motor from ezb? I would like to avoid the Ardino series of computers as I do not have any experience, compilers or desire to have multiple computers in this project. I am going to search Sparkfun for a control board but would really like a control board suggestion.
Sometimes it's just better to pay the money and do the easy way...
I found this clamp at Princess Auto today, it seems to have a 10" worm gear that could be salvaged to create a linear actuator.