
mcknight7424
USA
Asked
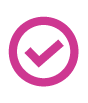
I have completed the printing of my inmoov robot. I was wanting to use ez-robot for my hardware and ARC . Will 1 ezb v4/2 be enough for the entire project or do I need 2? Also the hdd servos is that all I need, or is there any different servos that I need? Any guidance would be appreciated. Thanks in advance, David McKnight
Related Hardware EZ-B v4
That depends on how many servos, ADC ports and Uart ports you need. I'm not an Inmoov builder but I did build a full sized Lost in Space B9 robot (from the iconic 60's TV show). I used 3 full sized EZB's and one EZ-B IoTiny. Partly because because I needed more Digital and ADC ports then one unit could provide but also because I found it better for me to have EZB's in each section of the robot rather then running wires between three twisting, turning and leaning sections. I have the little EZ-B IoTiny up in the bubble that is connected to the torso with a small pipe that pops up and down and turns back and forth, two full sized EZB's in the main body and one in the lower leg section below the turning and leaning waist. I found the remote connection between several EZB's working together as one in ARC more practical then less EZB's and having to run cables from head to toe of a 7 foot robot that moves around at all joints.
So, take into consideration how difficult it will be to run wires between each level of your robot and count the different ports you'll need. This will tell you how many EZB's you'll need. These wonderful and powerful little units are so cheap, cost should't be a consideration. How much money have you already spent building your robot and buying parts and motors? If you're worried about spending money then another $100 or two really won't be a big thing considering it's the part that will be bringing life to your Inmoov. Done right, EZ Robot and ARC will make your life so easy and make you look like a engineering and computer genius.
@mcknight7424 For my fully built InMoov I used two full size EZB controllers, which is sufficient, but you could get away with one full size and one Tiny EZB controller.
Bare in mind that if you want to use ARC via a mobile iPhone/iPad device you can only control one EZB controller!
@Cem, Great advice. I haven't used a the mobile app yet and didn't know about only being able to use one EZB with one device. Is it possible to have two EZB's in one robot and have two devices with an app on each controlling the robot? I'd guess it's possible but I'd think that the EZB's couldn't work together like they can in ARC over WIFI.
@mcknight7424 I used one EZB Controller in the torso and two IoTiny one in each arm. I did this to cut down on the amount of wires going to the body to the arms you will need larger servos for use with lifting the arms and rotation of the arms you can use EZB hdd servos for the elbows if you build the Aerius elbow. Using three controllers does make it more difficult for setup. I find using the mobile app is way to limiting for use with this large of a robot, so I use a laptop, running windows 10. also You need small servos for the fingers I recommend using metal gear servos for this, just a little bit more expensive then the nylon gear servos but they are stronger. the picture shows the IoTiny in the arm just to the right of the servos and the picture shows the Aerius elbow, with EZB servo activating the planitary gear. the gear is printed in nylon filament. PLA filament just kept breaking under load.
As long as we'er talking about servo gears, Hitec offers servos with Karbonite Gears. I have several of these in my B9 robot arms. Along with being much stronger then nylon gears I find them to be much more quite then metal geared servos. Here's a write up on Karbonite Gears I found on ServoCity's website:
Karbonite Gears - Karbonite gears are relatively new to the market. They offer almost 5 times the strength of nylon gears and also better wear resistance. Cycle times of well over 300,000 have been observed with these gears with virtually no wear. Servos with these gears are more expensive but what you get in durability is more than equaled.
Here's the rest of the ServoCity write up on servos. I found this invaluable when I was picking out servos. Nylon and Metal gears are discussed at the end of the article:
Servo Terminology: Coreless Motor - This refers to the armature of the motor. A conventional servo motor has a steel core armature wrapped with wire that spins inside the magnets. In a coreless design, the armature uses a thin wire mesh that forms a cup that spins around the outside of the magnets eliminating the heavy steel core. This design results in smoother operation and faster response time.
Indirect Drive - This refers to the potentiometer inside the servo. The final output shaft (the part that the horn/arm attaches) has to be supported not only near the end but also deep inside the servo case. Indirect drive is when the final output shaft is not dependent on the potentiometer for support inside the gear case. Normally a bushing or bearing supports the load. Direct Drive is when the potentiometer plays a supporting role in holding the output shaft in place. Most sub-micro servos are direct drive since they are tight on space and do not have the room for an extra bushing or bearing.
Spline - This is the output shaft of the servo. It is what you attach the servo horns or arms to. Standard Hitec splines are 24 tooth with standard Futaba splines 25 tooth.
Transit Time - This is the amount of time is takes for the servo to move a set amount, usually rated at 60 degrees. Example: A servo with at transit time of .19 sec. to 60 degrees would mean that is takes the servo nearly 1/5th of a second to rotate 60 degrees.
Torque - This is the maximum power the servo can produce. It is normally rated in inch-ounces. This means that the servo can move this set amount with a 1 arm attached to the output shaft or spline. Example: A servo with a torque rating of 130 in.-oz. can move that amount with a 1 inch arm or slightly over 8 lbs. To convert in-oz. to pounds of force, divide this rating by 16. Example: 130/16=8.125 which is in pounds.
3 or 5 Pole Motors - This refers to the commutator in the motor. The commutator is where the brushes make contact with the armature. The more motor poles the smoother and more accurate the servo will operate. Most servos have either 3 or 5 pole commutators.
Nylon Gears - Nylon gears are most common in servos. They are extremely smooth with little or no wear factors. They are also very lightweight. If your application calls for long duration but not jarring motion, nylon gears are a top choice.
Karbonite Gears - Karbonite gears are relatively new to the market. They offer almost 5 times the strength of nylon gears and also better wear resistance. Cycle times of well over 300,000 have been observed with these gears with virtually no wear. Servos with these gears are more expensive but what you get in durability is more than equaled.
Metal Gears - Metal gears have been around for sometime now. They offer unparalleled strength. With a metal output shaft, side-loads can be much greater. In applications that are jarred around, metal gears really shine. There are two cons to metal gears, weight and wear. First, metal gears are much heavier than both nylon and karbonite gears. Second, metal gears wear several times that of nylon gears. How quickly depends on the loads that you place on the servo. They will eventually develop a slight play or slop in the gear-train that will be transferred to the spline. It will not be much but accuracy will be lost at some point.
I really appreciate the information. I plan to use a laptop running windows 10 instead of a mobile app or ipad. Also, I really like the Aerius elbow I just saw that last night. I believe I am going to re-print and go that route. Can I use the ez-robot micro servos for the fingers?
@mcknight7424 I have never used the ez-robot micro servos so I can't tell you how they would perform, but the full size servos are very good and I use them for everything. remember the aerias elbow is a real pain in the you know what to print and setup. I tried 4 dif filaments and most did not work I am using nylon for the gears now, but that is a challange to print. you need a high heat hotend and a bed temp of 100 deg. the weight of the arm can flex the large gear in the space between the four planitary gears and cause the gears to slip, soo the main gear cannot flex at all. no infill 100 percent solid. don't blame me if you flustrate easily.. but when you get it working it is amazing. inmoov can touch his head, try that with other elbows.
@nallycat
This whole project has given me anxiety lol. I am new to the ARC and ezrobot system so all of this is overwhelming. what kind of small servos did you use for the fingers?