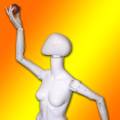
Zxen
Australia
Asked
— Edited
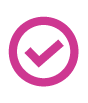
How do I plug these servos into the EZB please?
http://www.active-robots.com/high-torque-dc-servo-motor-60rpm-with-uart-12c-ppm-drive
(edited after reading the amperage draw in the datqasheet)
It supports several communications methods. Most reliable, least control (no feedback) is PPM, which is just like any servo.
UART would also work, although you would be limited in how many you use, and would need to do scripting.
I2C would also require scripts or a plugin, and is "quirky" to get working, personally, I would avoid it.
You will need 2 power sources, one for the EZ-B (7.4v recommended) and one for the servo(s) 11-15v since it draws more amps than you want to drive through the EZ-B.
For PPM:
Connect the ground of both power sources together.
Connect the 11-15v power to Terminal 6 (green) of the device.
Connect the ground from the EZ-B digital port to terminal 1 (black) of the device.
Connect the signal from the EZ-B digital port to terminal 2 (brown) of the device.
Use any servo object or script command to control.
For UART, see the datasheet for wiring and commands: https://www.active-robots.com/fileuploader/download/download/?d=0&file=custom%2Fupload%2FFile-1440671791.pdf You will need to use scripts and/or custom Movement Panel to send UART commands, but you can give precise movement commands and also receive position info from the encoder, which is nice.
Alan
nice combination (motor+encoder) with 3 different methods PPM/I2C/UART.
What you have is a motor with an encoder, or a continuous rotating servo.
using PPM (Servo) you will lose the encoder, and you don't have position control.
also bear in mind the following:
EZB controller is tailored and optimized for EZ-Robot servos, when you attach 3 party servos you can lose resolution (servo) or speed (continuous rotating servo).
EZB V3 pictures/values: https://www.ez-robot.com/Tutorials/Hardware.aspx?id=4
EZB V4 discussion post #14: https://synthiam.com/Community/Questions/9465&page=2
Motor documentation page 10 you can see the ppm values for your motor: Reverse max speed = 0.6 ms Stand/Neutral = 1.5 ms Forward max speed = 2.4 ms
so forward max speed is not possible to obtain, in most cases is not a problem unless you have a big mansion and your robot is speeding ...
I would go with I2C, that method allows reading the encoder positions can be useful for position/PID control.
Thanks so much. In summary, would you guys just add gears to a hobby servo to keep life simple? Or would you think about using servos like these in robot arms? After all, the shaft is centered and they seem to have a lot of torque.
Those look like a great device. I did a little searching to see if they are available in the US. Depends on your needs, budget, and how much you want to fiddle with scripting and dual power sources and such, but these really look good.
Alan
Thanks guys. Great analysis. I'll award the answer to thetechguru for this one, but I would like to know why people should avoid I2C. Don't they allow daisy chaining with just a couple of wires?
I2C is very sensitive to electrical interference and line resistance. You need to get the wire lengths exactly right, and there can be a lot of trial and error to get it working correctly. Serial communication is easy and reliable, and PWM is supported in all of hte EZ-B servo controls so you don't need to script every possible function you want to use the motors for.
Alan
High Torque Encoder DC servo Motor 60RPM with UART/I2C/PPM Drive http://robokits.co.in/motors/high-torque-encoder-dc-servo-motor-60rpm-with-uart-i2c-ppm-drive There are videos of the motor in use on this page.
I am about to invest in new servos to daisy chain together. Which method should I use? I suppose PWM is not a valid idea? DJ Sures says UART. What do you think?