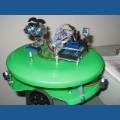
MovieMaker
I placed the tall robot on the Omni2000 base. I was told that if I put it backards, it would be more stable. Well, I did not try it the regular way, only backwards. It does not wobble at all. But, when I say forward, it creeps slowly. When I tell it go in reverse, it takes off like a ruptured duck, or because it is October next month, bat out of Hell. So, I am thinking about changing it back to original position so that it goes fast in the forward direction not reverse. I also put another IRON square from a second omnibot. So, it has twice the iron and three 12v batteries. It weighs a ton. Maybe it will work in the regular position. I also noticed that it does not do left and right correctly. on the right it goes Bump and moves about maybe an inch. On the left, it sort of turns left in a circle, not true left like 90 degrees as to what I expect. What do you guys think?
Thanks!
I have no experience with omnibots but it sounds like the motors may be overloaded or there's not enough torque to carry the weight.
by backwards, I mean REVERSE. I don't have a picture of the screen because I have got the robot apart awaiting the Neck,bezel, etc. I have taken off the netbook and I am getting ready to mount (I don't really know how) the W3 to the back. And the Mimo monitor to the front. The comment you made sounds bad. If they are supposed to be equal then I am screwed. That means a problem in the base. BUT, why do they go Forward and Reverse fine?
I don't have the pwm setup yet, I am just going with the Left,Right,Forward,Reverse.
Thanks to both of you.
OK, when I get it back together I will try that. Instead of using the movement panel, I use the pwm movement panel. I open the H-Bridge wiget (I haven't seen that one.) and use it. I remember assigning the H-bridge to certain ports. I am sure it will come back to me. I hope.
Thank You, my friend.
Depending on the H-Bridge you don't necessarily need PWM set up. You can supply the PWM pins with 5v and it's always 100% speed, most H-Bridges have jumpers doing that. PWM is only for if you want to regulate speed which isn't always necessary.
Have you tried the motors without them connected to the drivetrain? Do both motors work without problem in both forward and reverse with no load? Check this by applying 6-12v directly to the motor with no h-bridge, ez-b or anything attacked. It sounds like it could be an issue with the motors or the gearbox if it's jerky when moving, or possibly lack of power.
Incorrectly setting up the PWM (or not setting it up) shouldn't make it jerky when turning or slow when moving one direction but fast when moving the other direction.
I'd check the motors first, then check the drivetrain, then start looking at the H-Bridge and software, it's unlikely to be the software or H-Bridge from what I can gather.
Thanks, when I get it back together enough , I will check that.
I love this forum.
:-)
from experience i think the motors my be causing the different speed forward and reverse. they are brushed motors, so as the robot is driving forward it is tapering the brushes inside the motor toward that direction. As the motor is run in reverse its going against the wear pattern. it is the same gear ratio inside the gear box so the speed should be the same forward and reverse.
I don't want to have to replace the motors because it is a real pain for me. The gears go everywhich way. I am not mechanically inclined.
confused
you could try flipping which side the motor is on. so flip the left and right side motors. it wouldn't require any modifications