Asked
— Edited
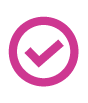
Hi all,
I want to tie and Double up 2 servos for more power. I'd like have the shafts will be tied together and facing each other. This means they would be turning at the same time but in different directions. Also they would be controlled through scripts. Is this the best way to configure them? I can see this may cause challenges in scripting and wiring. Any suggestions on how to set this up in ARC or have a better and different way?
A better way would be to use one stronger servo I would not try doubling them up as it may be way more problems than its worth and could cost you your servos
Wolfie, Thanks for the suggestion. I've looked and there aren't many stronger servos available for what I want to do. In fact I had hoped to use a RobotZone servo Gearbox and servos doubled up to get enough power to lift the arms of my B9. I also have limited room.
Gearbox
Here's the servo that comes with and fits this Gearbox:
Gearbox Servo
How you considered making your own servos or using a more powerful motor in the servo you have
Here is a youtube channel list that has some good info on how to make powerful servos HomoFaciens
If you are going to use two servos I would use some old ones you don't care about till you get the control scripts working right before you use good servos
Another thing to look into would be air pistons or hydraulics as they run a lot smoother than servos/motors
You can get servo doubler upper thingys which do just that if you wanted a hardware version, I don't know of any off the top of my head but if that's the way you want to go I'll try finding the topic which they were mentioned in. Josh may have an idea, I believe it was him who mentioned them in the past (from memory).
Or, you can use multiple servos in ARC. Check out Relative Servos or the Multi Servos in the regular horizontal and vertical servo controls.
Thanks for the ideas and input guys. I'm always amazed at how much help and good advice one can get from good people if I just ask. I'm still in the R&D phase of my B9 arm design and it's great to get input.
Here's a good YouTube vid where a guy shows two ways to tie two small servos together. The second example uses a type of "clutch" using stops and springs.
The Gearbox I pointed to in my second post almost does the job but struggles to lift the extended load (this is what the servo will lift when arm is fully extended). When I ordered it from servo City I had it geared fro 3-1 and they offer all the way to 7-1. However the higher the gearing ratio the slower the movement. I may get a gear set of 5-1 and trade off some speed.
Another way I could go is what @Wolfie alluded to; Make my own servo. I could find a strong DC motor like a small wheel chair or windshield wiper motor. I could control it through a Sabertooth/Kangaroo combo of boards like I have done my waist and hip motors. However I'd have to figure out how to mount an encoder or pot on the shaft and the scripting would be more complicated. Also to operate this combo I need to use Serial commands. I'll have other servos farther out on the arm to operate two directions of the wrist and the open and close of the claw. The native servo scripting in ARC would come in handy in animating the whole arm if everything were servos and accepting the same type of commands.
Another annoyance I'm experiencing is the "Whine" of the digital servo when it's energized and holding position or load. These HiTec Digital servos I'm wanting to use are programmable. I'm wondering if programming in a wider Deadband would help with this? Everything I've read says this is normal and unavoidable. It comes from the servo moving back and forth very fast and trying to hold it's spot. confused
Hey guys i have been on vacation and my ear was itching so i logged in.
yes double servos or more commonly called Tandem servos are a regular practice. There are some dos and dont's to follow here. A double servo is also the suggestion i made to Ant as well and he is now using them for lexis elbows.
Do-
Only use the same model servos! I cannot stress that enough.
try any use servos know for their power , here are some examples. Your budget will likely be your limitation. -hobbico cs170 $90 over 400 oz in @ 7.4 -power hd 1500mg $20 240 oz in @ 6v -hitec 645mg $20 133 oz in @ 6v
in a tandem setup you can either use script or a tandem servo controller from futuba. This makes one servo move in the exact opposite rotation from the other servo.
Do test your setup to ensure they are moving in unison and the servos are moving to the same but opposite rotation position. Once you are sure of positioning you can move to testing completely assembled.
Donts -
Dont even try mixing two different servos. Because of variations in position control , response time of the servos driver and the accuracy signal interpretation you are setting yourself up for failure to mix them.
Dont order any knockoff / clone or china servos if you can afford otherwise due to quality control in some cases. ( most servos are made in China anyways but it has to due with the quality control of the dealer channel you get them through) If you get unbranded or tower pro 995 servos then at least use two servos that were bought at the same time so they are most likely to have the same quality.
Dont hook up two servos in tandem setup with any stiff or hard linkage when you first assemble them and test. If the servos are off by more than 1.2 degrees ( i believe thats the number) they will burn up within the first couple min.