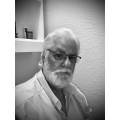
PRO
smiller29
USA
Asked
— Edited
MRB1 (My Robot Buddy V1) Project
Welcome to my MRB1 (My Robot Buddy V1)
I have removed the post because it was corrupted somehow and all the pictures and formatting was lost.
This post needs to be deleted.
hi smiller29
very nice project . wel explanned topic and great pictures . thanks for sharing .
Hi there,
I also have the Creality - Cr 10S pro v2 printer
my settings I use is:
"glass" bed = 87 nozzle = 237 speed = 20 to 60 max fan off Z = -2.29
I also use PETG filament - using the Ultimaker Cura 4.8 for settings, slicing etc...
good luck with your project - looks great so far
EzAng
What fun! It looks great! Please keep sharing. I'd love to see how those eyelids look in a vid when moving when you get it programed.
EzAng, I have made many upgrades to my CR10s pro V2, I use the Wham Bam printer bed, Micro Swiss 4.0mm Hot End, Bontech direct extruder. I use PrusaSlicer nozzle 235c Bed 85c The following are the key settings I use. I hope these may help others.
Dave, I will make sure to add videos once I get deeper into the project. Here is a link to the eye mechanism I used as a baseline for my remix.
https://www.instructables.com/DIY-Compact-3D-Printed-Animatronic-Eye-Mechanism/ Will Cogley has done a great job outlining his project and I would recommend you check it out.
Wow, wonderful design in that video. Looks lifelike.
I wish I were that organized! Right down to the connectors - wow
. This is going to be a fun build to watch.
DJ, Trust me if you saw my work bench you would see I am not that organized... But I hope to improve once I can get some of these parts put together. I just need to get a few more thing to start more of the assembly.