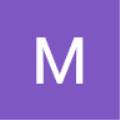
mbrooks
Australia
Asked
Would you pls give me a brief indication as to how I could use a 10k lin pot on my DC gear motor shaft presented as an analog input to EZ-b controller. My motor is driven by a Sabertooth (no Kangaroo present). Do you have an example tutorial you could direct me to pls?
Related Hardware EZ-B v3
You have two options...
1) I think what you want is a kangaroo for the sabertooth. Are you attempting have a motor work like a servo? If so, use the kangaroo add on from dimension engineering.
see my live hack with instructions here: https://synthiam.com/Community/HackEvents/Dimension-Engineering-Sabertooth-Kangaroo-19484
This is because the kangaroo is designed specifically for what you're requesting. Having any ezb firmware perform the same function will be a huge headache and undertaking. The PID control loop of managing a servo positioning is a lot more complicated than simply moving left or right based on the desired ADC range.
2) This is my preferred method. Remove the PCB from a servo and connect the motor output wires to the sabertooth hbridge direction pins. Then, power the servo pcb with 5v logic, because it will no longer be controlling a motor. It will now be instructing the sabertooth hbridge to move instead, and for that you'll want 5v logic.
I agree with all that DJ has to say.
I've tried in the past to control DC motor positions and speed through ARC with a pot attached to the ADC ports of EZB for feedback and the PWM control for speed. It worked but the code was complicated and the motor movement was mechanical looking. I struggled with smooth speed ramping, especially downward ramping towards the end of the move. In fact there were a few builders on this forum that gave it a try and none of us were happy with our ramping coding. Proper speed ramping between motor positions is important to get your robot's joints to move with human like motion.
DJ & Dave .. thanks both .. your points are well taken .. I will adopt the Sabertooth + Kanagaroo approach throughout
The servo pcb approach is much cheaper - and I find it to be a bit easier to configure. Check my tutorial for kangaroo - it’s a little difficult to setup
DJ .. agreed .. reckon I’ll have a go at your servo method also .. I could use the board from a cheap low power servo and I wouldn’t be restricted to Sabertooth.. I could use Clytron Duo-10 (you have already confirmed that Ark sees Duo-10 as a Sabertooth
Hi DJ .. so your method #2 .. effectively uses the servo board to give the Sabertooth the characteristics of a power servo ?? I would command the servo board in ARC as I would any normal servo but the Sabertooth would be driving the motors. I guess it is assumed that I would need 2 x such servo boards to manage the dual motor controls of the Sabertooth duals? Would you still expect to see all of Sabertooths control modes ie. dual mixed as well as individual motors? How exactly do I connect my servo outputs to the Sabertooth H-bridge direction pins? They are not broken out on Sabertooth??