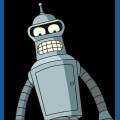
robotdude
Canada
Asked
— Edited
I'm trying to build a mid-size robot using the Thumper 4wd and two 2.5 Amp motor controllers and 12v/12Amp battery to run it but I don't have torque to turn it around (only to go forward/backwards). Actually I can easily stop the wheels with my hands. However if I will connect the motor directly to the battery I can't stop it from turning. So my guess is that the 2.5 amp is not enough or something is wrong. There is any quick fix for that on the 2.5 amp controller or should I get a new motor controller? Or. I'm pushing the unit to the limits Help..
I had a similar problem with my MiniB project using the RAD base. I had to go to a higher amp motor controller.
I'm not sure that I can do anything with the 2.5 amp controllers so I ordered another controller the Pololu Qik 2s12v10 http://www.pololu.com/catalog/product/1112 Does anyone know how to connect it to the ezb? Can I just use one of the hbridge controllers? How can I control the PMW on that controller?
Use the button switch on the motor controller to ensure it is using the power from the battery and not eZ-B
Interesting idea DJ. But the button switches are pressed on both controllers, but I'm still getting the same torque from all motors (but again if I will connect the motor wires directly to the battery it will be very strong and hard to stop with hand) Unless there is something wrong with the wiring. I used the video tutorial for the setup but the only thing I changed is to connect all the signals wires/5v/ground together to the same ports on the ezb (D15-D19). The 12v from both controllers are connected to each other and directly to the battery. I must get this thing up and running for an important presentation. I should get the new controller soon but I'm not sure if this will add to the complexity. Help...
I will post more pictures and hopefully video soon.
That thing is really creepy and really neat! Very interesting design, i like it
I'm unsure which direction the switch is supposed to be. I always forget
The motor controllers may not have supply enough power for that dude. You can most surely use a Sabertooth 2x12 or something, that will be enough. I have not heard many good things about the R/C Sabertooth versions, so beware of those. But the 2x12 or 2x25 in Serial Packet Mode is how we natively support the Sabertooth.
Other HBridges that provide more power will work also. I have found a few on ebay that support 50 amps per channel.
I'm certain your issue may be a limit to the 2.5 Amp Motor Controllers.
If the switch is pressed on one of the controller or both will make it move, but if both switches are unpressed then no power to the controllers. Should it provide power in both positions?
I already ordered a new controller the Pololu Qik 2s12v1 http://www.pololu.com/catalog/product/1112 how can I make this one work with the ezb?
Ok so I got the Qik 2s12v but I'm not sure how to connect it to the ezb. The Qik 2s12v have the following connections: Vin (out), gnd, err, rst, tx, rx, 5v (out), gnd , sin, gnd (rs-232), baud1, baud2, crc I think I need to. Connect the tx and rx to the ezb but I'm not sure where. Also, how can I control the pmw to the controller?