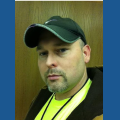
thegoodrobot
What is the input voltage range for my Hitec Servo?
All Hitec servos can be operated within a 4.8 - 6V (4 or 5 cells) range. Only the HS-50 operates exclusively at 4.8 volts (4 cells). Be aware that "coreless" and digital servos often perform poorly when alkaline batteries are used.
What signal do servos require to operate?
All Hitec servos require a 3-4V peak to peak square wave pulse. Pulse duration is from 0.9ms to 2.1ms with 1.5ms as center. The pulse refreshes at 50Hz (20ms).
What is the difference between coreless and cored servos?
In a standard motor like the one in the HS605 servos, there is an iron core between two permanent magnets. Around this core is the wire winding. The core generally has either 3 or 5 sections. As the core moves, these sections cause the core to hesitate slightly when it reaches a different magnetic polarity. This is called ratcheting. Because of this ratcheting, the cored servos have less start up torque and a wider dead band.
In a coreless servo, there is no iron core. There is one permanent magnet around which is a bell of wire. When electricity is supplied the bell spins around this magnet. Since there are no sections or core, there is no hesitation between poles. This gives the coreless servo better start-up torque and resolution.
What is the meaning of the wire colors?
On all Hitec servos the black wire is battery ground (negative), the red wire is battery power (positive) and the white or yellow wire is receiver signal.
What is servo deadband?
Deadband reflects the time it takes for a servo to respond when stick movement is given. Standard servos have a deadband of around 8us and high performance servos have a deadband of 1~3us.
If you have more servo facts that will help others, post here.
TheGoodRobot.com
As we have briefly discussed, RC servos convert electrical commands from the receiver back into movement. A servo simply plugs into a specific receiver channel and is used to move that specific part of the RC model. This movement is proportional meaning that the servo will only move as much as the transmitter stick on your radio is moved.
Servo Basics
All RC servos have a three wire connector. One wire supplies positive DC voltage usually 5 to 6 volts. The second wire is for voltage ground, and the third wire is the signal wire. The receiver talks to the servo through this wire by means of a simple on/off pulsed signal.
Sizes
Servos basically come in 3 different sizes (micro, standard, and giant or 1/4 scale) to accommodate the type of RC models they are being used in. There are slight variations depending on the specific application but for ease of explanation, these 3 sizes cover most of the RC servos out there.
Speed and Torque Ratings
Other than physical size, the next item that all RC servo specifications indicate is speed and torque.
Speed is a measurement of the time it takes the servo to rotate a certain number of degrees. This has been standardized in most specifications to 60 degrees; In other words, the time it takes the servo wheel to turn 60. The smaller the number, the faster the servo is.
For example a 0.12 sec/60 servo rating means it will take 0.12 seconds to rotate the servo arm or wheel 60. This would be twice as fast as a standard speed servo that is rated in the 0.24 sec/60 range. A RC helicopter tail rotor specific servo will have speeds as fast as 0.06 sec/60.
Torque determines the maximum amount of rotational force the servo can apply. This specification is measured in ounces per inch (oz-in) or in kilograms per centimeter (kg-cm). The larger the number, the more force the servo can exert. A typical standard servo will have a torque rating around 40 oz-in. A high torque specific servo can have torque values well over 200 oz-in.
So what exactly does 40 ounce-inches mean?
Well if you had a servo arm that was one inch long on your servo it would be able to produce 40 ounces of pull or push force at the end of the servo arm before stalling. If you had a 1/2 inch servo arm what do you think the force would be? Yup, 80 ounces of force. How about a 2 inch arm, 20 ounces of force - easy huh?
I should also point out that both speed and torque specifications are usually given for the two common voltages used for receiver battery packs. 4.8 volts for a 4 cell battery pack and 6.0 volts for a 5 cell battery pack. This also translates over to the typical BEC's or voltage regulator outputs if that is how you power your on board electronics. Obviously the 6.0 volt packs give slightly higher speed and torque ratings.
Even higher voltage servos are starting to make their way into the market with ratings up to 8.6 volts. These servos offer even more speed and torque and will continue to grow in popularity as 2S LiPo RX battery packs become more and more popular so no voltage regulator will be required. Assuming of course your receiver will operate at these higher voltages but most of today's 2.4 GhZ receivers are able to handle it.
The limiting voltage factor in the RC heli world is generally the Gyro and or gyro servo, many of which are designed to operate at no more than 5 volts; but as I said, that trend is changing and it seems every new gyro/tail servo or electronic flybar system are now rated at 6 volts.
Digital Servos vs. Analog Servos
Now onto the real meat and potatoes of this RC servo discussion.
Up to just a few years ago, the only RC servos available were analog, but now we have digital. To answer the question of which is better for RC helicopters or planes and cars for that matter let's look at how each work and the choice will be pretty obvious.
First off, there is no physical or main component difference between a digital servo or analog servo. The servo case, motor, gears, and even the feed back potentiometer all have the same functions and operations in both types.
The difference between the two is in how the signal from the receiver is processed and how this information is used to send power to the servo motor.
A lot more info at: http://www.rchelicopterfun.com/rc-servos.html
Too much to copy & paste! I thought this info may helpful. TheGoodRobot.com
Nice!