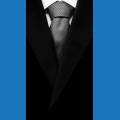
Perses
USA
Asked
— Edited
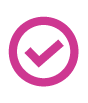
Following the instruction video, i was able to set up the Hbridge L298N RED
the problem im facing is, it only controls the read motor, not the turning motor.
the video online shows dj setting up just one motor. am i missing something?
Not really sure what you mean by the read motor and turning motor to be honest but if you read through the L298n tutorial I wrote it tells you everything you need to know about these H-Bridges.
sorry, typo. rear motor not read motor.
on ARC when i hit right, left, up, down they all control the back motor (forward /back)
the front motor (right left) stays idle
First, you are planning to use the H-Bridge differently to how the H-Bridge Movement Panel is designed. I presume one motor is intended to drive the car and the other will turn the steering however if this is the case you will probably be disappointed with the results and possibly even cause damage to the steering. The H-Bridge has no feedback therefore doesn't know where the motor is. It is not suitable for such a steering design. Use a servo.
Both motor channels are used for drive wheels. Both move forwards to move the robot forward. Both reverse for reverse. One forward and one reverse causes turning and the opposite for turning the other direction.
Secondly, and I don't mean any disrespect by this at all but it looks like you have almost ruined that H-Bridge with the soldering. Really no offence is meant here but sloppy soldering (and burning/melting of the insulation and plastic parts) can be dangerous, can cause shorts which can lead to unwanted results or even fire. Use jumper cables and plug in to the pins if your soldering skills are not great.
haha, didn't know the camera has such good detail. In my defense, I bought a bunch of them from ebay. I Just wanted to test out with one before I rewire everything to fit. prototypes usually start off looking ugly. So if its ruined, it only cost me a dollar.
How would you handle the front wheels in this case. After all, the manufacturers of rc vehicles all use similar motors, and they managed to not 'damage' them somehow.
As you can see in the following examples (and tons of others online) an h bridge is used same way as I'm trying to configure it
Back to the question though, Why does Right and left on ARC control same as up down(second motor) , instead if controlling the first motor
The H-Bridge in ARC is set up for the most common type of drivetrain configuration which is two motors, one on the left and one on the right.
To move forwards both motors spin forwards. To move reverse both motors spin reverse. To turn left one motor spins forwards and the other in reverse. To turn right the motors turn opposite to how I described turn left. This is all in the post I linked to previously.
All 4 directions on the H-Bridge Movement Panel cause a different response from the H-Bridge. Right and Left do not do the same as forward and reverse (or up and down as you put it).
All 4 directions will make both motors move in one direction or another as previously described.
If you want to steer by turning the angle of the front wheels you will need feedback of some kind. You could add in a pot, you could use switches etc. but the easiest, cheapest and quickest method would be to use a servo for this. You would then need to use a custom Movement Panel and script for movements.
Sounds like the most common setup is a tank or tricycle
Thanks Rich, It clears some things up.
I still find it funny how a low level audrino can handle the hbridge in the way i want it as depicted in the above videos, while ezb can't.
Also, I'd like to use the onboard RC Battery 9.6v
Do you know if that will break the ezb v3a
I highly doubt an Arduino can drive a steering motor without pots ir encoders to tell it the motor position. Virtually all RC devices use servos for steering bwcause they have precise position control and end limits so tje motor doesn't spin your steering wheel off.
Using a custom movement panel, your h_bridge to drive the rear motors and a servo for steering, the EZ-B can certainly do what you are trying to do.
The v3 can handle 9.6 volts input, but it regulates down to 5v on all of the outputs, so might get a bit hot, but won't damage it.
Alan