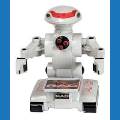
PRO
rz90208
USA
Asked
— Edited
I have 2 EZBv4 controllers that D12-D23 do not work. The first one stop working a few weeks ago and now the second one. I have tried doing a reset with the reset button but that didn't help anything else I can try? if not is just the controller board available?
RichardZ
Hi RichardZ,
Were the two EZ-Bs placed into the exact same application? What is usually connected to D12-D23? How are you testing these ports?
You could try taking the EZ-Bv4 enclosure off and re-seating the WiFi board on the main board. Separate the two boards and them put them back together, just like in this video:
Jeremie, Sorry for the delay in responding, I was at a county fair showing my Inmoov as a static display. Both EZB's are in the same Inmoov. But the second EZB ports stopped working before I put it in the Inmoov. The InMoov is powered by a 60 amp Dell Server Power Supply. I take the 12v from the power supply and that powers both EZB's. The 12v also goes to 2 - 25 amp 6v regulators that supply power to ALL servos. All grounds are tied together.
I have tried reseating the communications board on both.
RichardZ
Hi again RichardZ,
To test each port you could make a new program and hook up an LED to Ports D12-23 and send a simple signal like a digital high and low? (Just make sure you have the LED cathode to Gnd and Anode to the digital port)
Do you own a mulitmeter? You could use that as well to see if there is a signal at the Digital ports or if power it's getting to the D12-23 Red power pins.
Yes, I have a good multimeter. I will do the high/low test first and depending on how that turns out, I will compare D12-D23 sinewave output to a working port with my O'scope.
I will post my results.
using the following basic code, I checked each port and had no change on the white (data) pin. 0v
What was connected to those ports?
805BB Servos, and drew power from a separate buss not thru the EZB.
@rz90208 I could be wrong but I thing @DJ means what was attached to those ports when you did your set(D12,ON) tests....