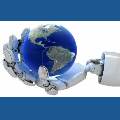
Jerome
France
Asked
— Edited
Hi,
I bought a double H Bridge Drive, here :
I saw this DJ's tutorial
But I don't understand how connect Ez Board and this H Bridge, because I don't Vcc port on H Bridge.
I did some testing, but I have only one engine running
Can you help me ?
Thank you.
Jerome
I believe the +5V is the VCC on the H-Bridge. VCC on the EZ-B is 5V so it would make sense.
Vcc is your input voltage for the motors. +5V is power from the H-Bridge to the EZ-B. It can be enabled/disabled by jumper on the H-Bridge.
In the E-Bay auction pics Vcc is labeled +12V.
Hi,
I don't understand, if I connect Vcc input voltage +5v on EZ-B or not, it's the same result. I have only the right motor works ! (and it works very good, but the left motor doesn't works) I reversed motors and it's the same result, only the right motor works). Some pictures for you of my mounting :
I don't understand, why if I connect or not the +5v (Vcc), it's the same result ? why I have only the right motor works ?
Can you help me ?
Thank you
Jerome
An another picture better
Jerome,
Where is your PWM line?
Have you connected it as per DJ's video?
Also, what are those motors rated for power?
They look quite big and might require more juice than the EZ-B power pack can supply.
1 = gnd 2 = +5 3 = ext
I have the same h bridge this is how I have it wired. to enable the PWM you have to take off the ena & enb caps and only wire it to the first pin
Jerome,
I'm not acquainted with this Motor Controller. However lets see if we can work through this.
First possible explanation: In your photo above I see the A and B enable pins. It looks like you only have a lead going from EZB to the B enable pin and appears to be the right motor now seems to be working for you. The diagram you drew above shows a jumper between A & B enable which you DO need to get both motors to start up. That way you only need one digital signal port on EZB and one PWM control set to that port in ARC to control the speed of both motors. Make sure you have that jumper installed and the lead going back to EZB is indeed on a digital signal port that is set properly in ARC.
Second possible explanation: This board is not able to be controlled by PWM. All you can do is enable or disable each motor using the jumper block.
Third possible Explanation: You have everything wired up properly and you have overloaded one side of the bridge and burnt it out. Did that side ever work? you can quickly blow one side of an H-Bridge by quickly reversing the direction of a DC motor. This controller is only able to handle a 2 amp load, (3 max). Start up amperage and quick reverse amps can be higher then what the specs are for the motor. Sometimes twice as high! So if your motor is pulling almost 2 amps and you quickly reverse, it may send up to 4 amps back into your control circuit. Is your controller is rated only for 2 amps you have a problem. To protect ageist this you need to buy a controller that already had over voltage and reverse protection or build a diode protection circuit that will draw off that fly back voltage to ground. I see there are indicator lights on the controller board. One light should come on for each direction and each motor. Is that happening?
One thing; I see different wiring in each of the pics you show. You need a ground connected between your power supply (the Negative) , EZB (Negative on it's power port) and your Controller (Power Ground between the 5v and 12v power input). I think if your using 5v from the EZB you need to remove the 5v enable jumper block. If your using the power pack you need the jumper block installed. This would also be the case if you use another type of external power supply like a 12v power converter. From the Ebay link you posted: "This module has a built-in 5v power supply, when the driving voltage is 7v-35v, this supply is suitable for power supply, DO NOT input voltage to +5v supply interface".
Another thing; Lumpy is correct, your motors may be to big for that little power pack. Consider using a different power supply that can supply more volts and amps. What are you going to use this in? Are you able to use a power converter you can plug into a wall? An old computer power supply is a good choice for bench testing. Once you get the bugs worked out you can find a proper battery set up that can provide dedicated power to only your motors. That way you can give 12v to your motors and 5v to your electronics through a step down board or EZB it's self.
Try this:After you have rechecked and rechecked and rechecked your wireing and power supply remove your motors from the controller. Attach a digital tester to see us your getting the voltage you expect both A & B output terminals. Don't hook up any motors till you get the power readings you expect. If you don't own and know how to use a tester now is the time to buy one and learn to use it.
Good luck, Dave Schulpiug
@Lumpy I use 2 motors of windshield ice. I thank to use it with an another battery 12v. What's the PWM line ?
@derrick Thanks for your pictures. My error is definitely I don't use ENA and ENB, because I don't know what is it ? And how to connect it (which connector ? (link on web, please).
@dschulpius Thanks for your answer. In first, I'll test with smaller motors, and I'll see ...
Jerome