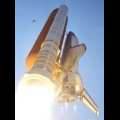
ndavid79
I'm seriously considering investing in a CNC mill, specifically a Probotix Fireball V90. It can machine plastic & wood in upto 12"x18"x2.5" pieces all day long and cut light aluminum to shape on occasion. I'm severely disabled, on a ventilator even, so can't really get out in the garage to build stuff without help, but consider myself a good technical designer in CAD. Cutting parts for my robot & woodworking will be its main job for me.
I've got ideas for custom pan/tilts, small linear actuators, custom drive tracks, & a self connecting charging station.
Anyway, this will be one of the biggest purchases I've ever made, makes me kinda nervous... So I'm looking for ideas for things I can machine & sell in parts form to at least partially help my payoff strategy.
Certainly custom control horns, Mounting boards for servos, motors, etc. You might be able to build blanks for chassis, bread boards, break-out boards, etc.
Beyond that, if you have concepts for whole kits, that would be great.
Generally speaking, from a retail standpoint, accessories and parts will have greater markup latitude, and because of the more generic use cases, have greater retail penetration.
(my .02)
{.02097 CN)
ndavid... you could make all kinds of things.
I could build a website for you where people could upload their own cad drawings or have you do one for them.
You could make bases for robots. It's hard to find one. they're either big or small no in betweens.
Kits would be good. You cold make kits all day. Wooden boxes, display cases.
Where are you located if you don't mind me asking?
Samantha
I'm in Central Arkansas. Email me sometime, nlkdavid at pinnacle175 dot com
So right about the no medium sized robots, the toys are either to small or to expensive. One of my motivations is actually a decent sized EZ-B'd Wall-e, kinda half way between the toys & the full sized ones from The Original Wall-e Builders Club.
But my big bot I'm thinking along the lines of an Omnibot 2000 clone, but upsized close to 100%.
It's here, now its assembly time!
Wow! I've always wanted to get one of those. This one looks reasonably priced...I guess.... sick Is it hard to learn how to program? Do you just have to create a CAD drawing then load it into the CNC and it cuts the part per the drawing? Or is a lot more complicated than that?
Rex
Rex,
Yes that is pretty much exactly how CNC's work with CAD drawings.
I want one....
Samantha
That's the jist of it, thought it's really a 3-4 step process utilizing 2-4 programs depending on what your doing & the amount your willing to pay for the software. The steps are: CAD (Computer Aided Design)- draw what you want to create
CAM (Computer Aided Machining)- convert your drawing into G-code, machine readable code that tells the machine exactly how to move.
Post Processor (for advanced machining) - if your machine has more then 4 axis, you pre-program this with the machine's dimensions & geometry and it adjusts the G-code to how your machine needs to position everything to get the end-mill (cutter) exactly where & at what angle it needs to be.
Controller - in the hobby world, this is normally a old desktop computer with a parallel port, running Mach3 (windows) or LinuxCNC (formally EMC2). This takes the G-code, which is encoded in inchs or mm & degrees (for rotary axises), calculates that against the number of steps per unit your machine's drive system requires & drives the machine's stepper motors accordingly.
CAD & CAM are sometimes combined into a single program or into a program + plugin. For flat surface machining & cut out work, called 2.5D, there's actually 2 free combos, Google Sketchup + the Phlatboyz's Phlatscript plugin and Inkscape + the G-code Tools plugin. Then there's 2 more capable/somewhat affordable ones I'm looking at, both are $150 each, CamBam & ArtCAM.
For 3D work, combined programs are quite expensive indeed. So what I'm going with is a combo of (for CAD) Google Sketchup + the DXF/STL export plugin, FreeCAD, & probably Alibre Design Personal Edition ($160), feeding (for CAM) MeshCAM (which I got bundled with the machine for $99 vs regular price of $175-$250). With these I can do 1 or 2 sided 3 axis machining & 4 axis machining. Past that, a CNC software stack can run in the thousands.
Very good kit this... 85% done in 2.5hrs!