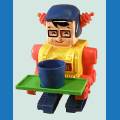
Mulberry
USA
Asked
— Edited
Hello All
So I'm a total novice at electronics and am on a steep learning curve so bear with me :-) I'm using EZ-Robot to control my B9 and have a question about H-Bridges. EZ recommends the L298N. I've reviewed the tutorial (see below) and think I grasp the process. What I'm unclear on is how much power the board can take. In the video the power source used is only battery. My system is 12 volts. Is that within the specs and how many H Bridges could I route through a single board?
https://synthiam.com/Tutorials/Hardware.aspx?id=25
Thanks,
Daniel
It will handle 12v like a champ. I am not sure about the amount of H-bridge, but my guess is one
Well, yes, EZB will run nicely on 12vdc. I have three EZB's in my B9 and all are running off 120v AC to 12v DC power converters.
Your EZB can run as many H-Bridges as there are digital ports. Depending on what style H-Bridge you get will depend how may ports each H-Bridge will take up. Some H-Bridges will only control one DC others will control more. The L298N sold here will control 2 DC motors. You can figure Two digital ports per DC motor. So, EZB has 20 digital ports, you can run up to 10 DC motors. Of course that means you wont have any ports left free for other things. When that happens it's time to get a second EZB.
EDIT: I originally said one port per DC motor. I forgot that you need to figure that each direction of the DC motor needs a different Signal wire meaning you will need 2 Digital ports per DC motor. I changed it in the above paragraph.
Remember the EZB is only powering the control circuit and trigger signal of the H-Bridge. The H-Bridge it's self is doing all the heavy lifting and should be sized to the current of the DC motor your controlling. The L298N sold here is a great little H-bridge for small DC motors, I use it is contorl the 2 small DC motors that rotates the radar and sensor ears on the head section of my B9. However I burnt up 3 of these when I tried to control the much bigger DC motors that operate the waist and hip rotation. Although the Amp specs were within the 4 amp max of the L298N the problem came in when the DC motor reversed. Fly back voltage created by the magnetic collapse of the coils in theDC motor throws back up to twice the original voltage into the H-Bridge. So I ended up buying a nice h-bridge from Pololu with a higher current rating, over voltage and reverse voltage protection. It's a VNH5019 Motor Driver Carrier and a good choice for your B9. If your using 24v batteries this is not a good choice do to the over voltage protection. Here's the link: http://www.pololu.com/catalog/product/1451 . It will only control one motor at a time. Here's a good choice if you want to control 2 DC motors from one H-Bridge. However it does not have a populated Current Sensing section: Dual VNH2SP30 Motor Driver Carrier MD03A - http://www.pololu.com/catalog/product/708 .
Good luck and have fun! Dave Schulpius
Thanks for sharing Dave!
..bad experiances are a teaching benefit as well! "dont eat a molton marshmellow"
Ya, I got a lot of bad experiences I can share. Sometimes I wonder if I'm learning anything from these "Teaching" moments as they keep happening. blush
Well, as an old mentor used to tell me; "What you don't have in your head, you make up out of your wallet".
I've had a lot of people ask me how I know how to do all this stuff. I just tell them I don't have enough money to pay someone to build the things I want or fix the things I break and blow up so I have to try to learn how to do it myself. Sadly sometimes I don't learn fast enough and have to fix things two or three times.
Well I am in the same classroom in the "school of hard knocks" ..or soft black smoke ! another old saying wich I am sure your familiar with ..."old too soon smart too late" but WE have to break that one
Dave have you thought about using a "projector" to cast out a cool visual from a color lcd...I recently found an old slide projector..something I am sure technopro has only seen in a museum
at a Lions sale for 5$ which I am going to incorporate in my robot...heres the link....in case your interested..
Projector
Nice find! No, I hadnt even considered this. However it's a very neat idea and something I need to consider.
Thanks!
Afternoon All
So I'm working with the single Pololu H Bridge VNH2Sp30 to operate a 12volt Dewert motor to rotate my robot left and right. My understanding was I only needed the white wire from my EZ Board to control voltage and then my + and - will tide to my outside power source but when I read the instructions on the board specs (http://www.pololu.com/catalog/product/706) it says use connection A and B to control the direction of the motor. How would that work if I only have a single white wire? Could it be I run two white wires to my EZ Board and then have a left and right control on the EZ interface? I'm attaching an image of the board.
Any advice would be greatly appreciated.
Thanks,
Daniel
Edit. See next post.