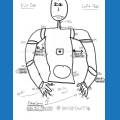
Dunning-Kruger
Canada
Asked
— Edited
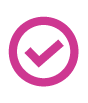
I know sensors like pings and IR will need a 5V regulator inline if you put more than 5V through the V4 board... Just noticed my sabertooth motor controller also uses a 5V input line in addition to the signal line and ground line... Does this mean even motor controllers will need a 5V inline reg as well? I tried removing the +5V wire from the sabertooth (in other words just leaving the signal and ground attached) and it still seem to work fine at controlling motors... Just wondering what will need 5V regulators and what won't...
Thanks Richard
@Richard,
Take another look look at the manual for your Sabertooth. I think you'll find that that 5v connector on the signal side is an "output" connector. The 5vdc is created right on the Sabertooth by it's own power converter. You can use this output voltage to power other units that need 5vdc right from your Sabertooth.
Well, that makes sense... LOL... Now I at least know the +5V connector on the sabertooth is 5v tolerant... Duh.... Thanks Dave
Easy mistake to make, I've seen posts from others about other controllers that also have +5V outputs (and the sabertooth) where they have assumed they are to be supplied with +5V. And I'm not surprised, a lot of other things have +5V which is their supply in.
But it's a good example of why you should always check and double check the datasheets
I do feel a little stupid now for not reading the manual thoroughly... If not for my curiosity and thanks to Dave I might have blindly plugged my sabertooth into the v4 board with a much higher voltage on the output pins...I was actually in the process of making a custom 5v cable for plugging in sensors to the v4 board...
If you learnt from it then it's not a bad thing. We learn by making mistakes
Don't feel stupid. Heck, I hooked the 5vdc port pin into that same "output" connector on the Sabertooth the first time I wired them both together. Thank goodness nothing bad happened when I powered it all up. eek I caught it later when nothing was working like expected and I reread the manual. blush
Good work , just a tip , keep a bag of heatshrink handy. It makes insulating custom wiring easier and safer than tape. It gives your wire a professional look too.
I was making an inline 5v sensor cables when I had noticed my sabertooth still connected to 5v pin on the ezb .... Thanks Rich