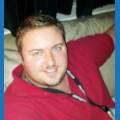
jstarne1
USA
Asked
— Edited
ANT is doing a great job getting the first proto of the XLR6 ready to send to me to start working on so for the sake of planning I would like to listen to the communities ideas for a rover kit and rover base. The EZ Robot kit is a great place to start so we aren't trying to replace Roli. This is for the next level kit , more ridiculous add ons can be made later. I will share some of what we have in mind so far. As always all our projects are being developed for use with ez robot Ezb v4 but you can still use a v3 in them.
Rover kit , that's a top and bottom to make the whole Xl rover
- misc parts like wheels
Rover base only, that's the bottom half of the Rover frame with wheels and a flat tray on top all molded from 80A shore urethane plastic
The Zero Degree Rover
want to go fast? Driving a skid steer base is difficult but you can switch modes. Lock the rear in place and turn only the front servos. ZOOOM...! This versatility is not found in any other rover base kit. 6Wd and individual motors for each wheel give power in a small package without noisy plastic gears. Gear reduction comes with its own problems. The motor pods are for a 40mm Nema 17 stepper. Alternate mounts can be swapped for 58mm Nema 23 steppers or even continuous standard servos. This is the staple of modular versatility!
This is Cool! How would you mount the motors? Hinged? spring loaded? EDIT: One Idea I got was to do a 4WH drive version. this is my concept of this in 4 wheel.
If you use it, go ahead! But give a shout out to me.
I really dig the two driving modes via locking the other ones in place. nice work so far josh.
Just some little tests , i poured out a few ounces of the plastic in to a square so i could test things like deflection under pressure. This is 6000 psi tensile strength urethane. The thickness is a hair over 1/4 thick. The pattern in the middle was from where I moved the mold right after pouring. This stuff hardens in 90 seconds so it literally changed from dark brown to tan in seconds. It's good to let it sit for a few minutes to cool. The temperature jumps to around 250 degrees when it changes color so i let the stuff cool a few minutes.
Obviously parts inside a mold come out perfect. What I have quickly learned is its not required to have super thick walls with this material.
Here is the test square popped out of that mold. The masking tape is stuck to the back which is fine because I am just testing strength of the material. At this point trying to bend it with hands and legs didn't work. This is super tough material!
@jstarne1-XLRobots.com Josh, where do you get your urethane at, is it available in stores or do you buy it somewhere online, just wondering :-} Steve
You can get a similar product from hobby lobby two part liquid plastic casting resin. 28 ounces is 25 to 30 dollars. Obviously if you buy larger amounts the cost per ounce drops. If you decided to do something custom get yourself a accurate scale. It's much easier to pour into a mixing container by weight than wasting measuring cups.
@antron , thanks by the way. If the base of this rover didn't have the plus features like this , it wouldn't be any better than the ones already out there.