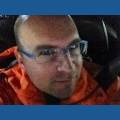
mcbaker01
USA
Asked
— Edited
Do I need one controller per motor or one controller per side?
In another thread, DJ said, "one controller per set" but in the same paragraph he said "running multiple motors (in series or parallel) is a bad idea"
Are the 2.5A controllers enough? Apparently this thing draws 14A max.
Is there a controller I can get that will manage acceleration, turning, motor braking? Is this a better way to go?
I think I may have figured out what he meant.
I'm guessing the L298N has two motor controllers on each unit...
So two L298N controllers is actually 2x2=4 motor controllers.
So my only remaining question... wouldn't this: http://www.pololu.com/catalog/product/1376
be better than L298N in terms of meeting the max current draw?
Oh... so sorry, I think too many assumptions of your experience have been made eek
Yes, most of the H-Bridge controllers we have been referring too are dual channel (aka Left and Right motor control) and the amperage specs are usually based on a single channel.
I think that the controller you mention would work better but would need to be controlled via the TTL method (I think)... no experience there so hopefully someone else can add to this... or suggest another better controller.
Addendum: I really want one of these (actually the 6WD) and have been looking into their capabilities, but not looking at the specs as close as I should have been
You are correct in that the recommended controllers should be rated at 14A per channel (single motor) to cover all usage potentials. I would then go as far to say the I would not personally attempt to use the 2.5A controller for anything outside of bench testing.
As per quote on www.Pololu.com
"The motors are intended for a maximum nominal operating voltage of 7.2 V (2V minimum), and each has a stall current of 6.6 A and a no-load current of 420 mA at 7.2 V. Since the motors will briefly draw the full stall current when abruptly starting from rest (and nearly twice the stall current when abruptly going from full speed in one direction to full speed in the other), we recommend a motor driver capable of supplying the 14A combined per-channel stall current of these motors at 7.2 V."
And for your last question, I personally like THIS controller, as previously mentioned in your other battery post, to cover all features like acceleration, turning, motor braking, etc.
That's an entire micro-controller isn't it?
Seems overkill in combination with ez-b. lots of replicated functionality ?
Yes, as mentioned earlier, it is a bit of overkill in that aspect but I wouldn't put its ease of use or functionality (micro-controller wise) in the same category of EZ-Robot
But for the reasonable price, it offers all the motor control features you could want or need for that platform.
And as a bonus you could use (independently on some things, or in conjunction with the EZ-B) or ignore what programmable functions it does have and use EZ-B as the master controller, or just use as a simple RC "car", etc.
Of course, as I read it, one doesn't have to use the micro-controller... I am still researching that and could be mistaken
... and there are probably similar motor controllers sans-microcontroller out there, but that's the one that catches my eye for my want list
Hi, I'm using the 6wd version in my project. As for powering my motors I'm using a sabertooth 2x25a (50a burst). And I control it in r/c mode. You can probably power your 4wd version with either a sabertooth 2x12a (25a burst), 2 rc escs with about 20a each or any other type/brand dual h-bridge speedcontroller that supports the required current of your motors(always make sure your controller can offer more than you motor requires else you will roast them).
The nicest way to actually controll it would be by controlling each motor separatly(like with the 2 dual h-bridges recommened by others, but then those that can handle the current). Ideally you would want this with the 6wd version, then you can make the nicest/realistic smooth turns. You can do this by differing power to each motor. But with 4 wheels you wont have the other 2 wheels that slow down the other wheels while making turns and I dont think you will notice the difference when powering the motors separatly or just parallel/series.
Some time ago I made a thread about rc escs, its a little bit dated because of all the updates, but the base remains the same for every motor controller. Rc esc thread
Hope I helped! Or atleast did something.
Idea for the future: It might be smart to make an unchangable thread that contains the base information about picking motor controllers, servos, sensors, etc. So people know what they are buying or atleast what the need for their project.
I went ahead and ordered the Dagu controller. It was only $75 on amazon.
With that Dagu controller you will have to wire the right side motors in parallel and the left side motors in parallel, right? Doesn't that go against the advice that "running multiple motors (in series or parallel) is a bad idea"?
@Mike. It can get confusing can't it
That's why advice alone can't cut it, research is required... and lots of questions
Running motors in series is not recommended for most robotic drive applications due to voltage and amperage issues if one motor stalls causing issues with the other motor(s) in series.
However, running motors in parallel is not only fine, it is rather common in multi-wheeled (4+) chassis that use skid steering, provided they are of same voltage, amperage and preferably make and model.
Dagu is the company that makes both the Wild Thumper and the controller I pointed out... in fact that controller is specifically made for those series of chassis, thus will work just fine with each side wired in parallel. Here is a clip form the main retailer Pololu
"This is a differential-drive chassis, meaning that turning is accomplished by driving the motors on the two sides of the platform at different speeds. The two motors on each side of the robot are wired in parallel, so only two channels of motor control are required to get this chassis moving. The motors are intended for a maximum nominal operating voltage of 7.2 V (2V minimum), and each has a stall current of 6.6 A and a no-load current of 420 mA at 7.2 V. Since the motors will briefly draw the full stall current when abruptly starting from rest (and nearly twice the stall current when abruptly going from full speed in one direction to full speed in the other), we recommend a motor driver capable of supplying the 14A combined per-channel stall current of these motors at 7.2 V."