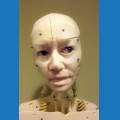
3dGuy
Canada
Asked
— Edited
Hello All those smart than I.
I am trying Digital giant scale servos on my Inmoov -
HS-5805MG Giant Scale Metal Gear Digital servo Motor -
and boy do they whine when not in use. Yes, I have tried auto release and manually releasing them from a movement window.
when 4 of them are active and then stationary the whine is unbearable.
The only way I have found to quiet them is to cut the power.
Anyone have any experience with these?
I have tried various voltages from 4.8 -6.0 v
You're not going to stop this noise. It's inherent in digital servos. The bigger the digital servo, the louder it whines.
What's happening is this: When the servo is stopped in position, the control board inside the servo is getting feedback from the pot and is constantly switching directions to keep its commanded position. That switching back and forth is the whine you hear.
The only way to stop the whine is to have a servo that has a wide deadband and be lucky enough to stop the servo in it. Of course any weight on the servo will pull it down and cause the servo to start whining again by switching to try to maintain it's position. Your servo is programmable. Perhaps you can play with widening the deadband to see if this would help some of the whine.
I agree that this sound is unacceptable in a robot. There are motor controllers that use ultrasonic switching. The switching happens at such a high frequency that you can't hear it. I use a HS-7950TH servo inside of a ServoCity gearbox for more power on the forearm of my B9 Robot's arm. When stopped the gearbox helps support the servo sometimes inside the deadband when at rest and I could get the servo to be quiet. Most of the time it didn't help the whine though. I decided to gut the control board out of this servo and replace it with a Pololu jrk 12v12 ultrasonic motor control board. The result was complete silence and as an added benefit the servo can now hold position all day without overheating. This is definitely a very expensive way to do it but if you're spending tons of money already on a large robot then this expence is just part of the price you pay if you want silent servos. Here's a video I did of this surgical procedure. I mention in the video that the servo heats up. I had a damaged servo in this vid but after doing this mod with a good servo it runs cool. Also I mention the servo not holding position. There is a breaking feature in the software of the Pololu jrk 12v12. When enabled the motor holds position exactly until power is switched off. :
Another thought is to have your servo stop in a resting position where gravity won't move the servos. Then quickly kill power to them or releasing them. You can easily release them with the release command after your animation routine is complete. As long as you don't pause the servo movement too long between moves you shouldn't hear the holding whine.
One more thing. Metal gears in a servo are noisy when they move but very strong and last longer with heavy loads or jarring actions. Karbonite Gears are almost as strong but much quieter. Nylon Gears are very quiet but don't last as long as the other two choices under heavy loads and won't handle a lot of weight. Here's a write up on these gear sets I found on ServoCity:
Nylon Gears - Nylon gears are most common in servos. They are extremely smooth with little or no wear factors. They are also very lightweight. If your application calls for long duration but not jarring motion, nylon gears are a top choice.
Karbonite Gears - Karbonite gears are relatively new to the market. They offer almost 5 times the strength of nylon gears and also better wear resistance. Cycle times of well over 300,000 have been observed with these gears with virtually no wear. Servos with these gears are more expensive but what you get in durability is more than equaled.
Metal Gears - Metal gears have been around for sometime now. They offer unparalleled strength. With a metal output shaft, side-loads can be much greater. In applications that are jarred around, metal gears really shine. There are two cons to metal gears, weight and wear. First, metal gears are much heavier than both nylon and karbonite gears. Second, metal gears wear several times that of nylon gears. How quickly depends on the loads that you place on the servo. They will eventually develop a slight play or slop in the gear-train that will be transferred to the spline. It will not be much but accuracy will be lost at some point.
EDIT: Something else I found for your reference and comparing against your application: Note: Be aware that high vibration gas (not glow) engines combined with large control surfaces and large throws (3D models) can put undue strain on the gears. Metal geared servos are recommended for these applications even if under 12lbs. Warning: Do not use thread lockers on Karbonite geared servo as it will cause the output shaft to fail.
Thanks Dave. That was a lot of effort you did for me, I really appreciate it!
I have ordered a servo programmer so I'll see if the dead time can be tweaked.
They do whine when released and no pressure against them.
There are a few interesting Programmable Features other than dead band you can set to on your servo. I really don't know how they would affect the whining you're having but if you play with them and study what these are they sound like they may help:
EDIT: I see Aerius posted a project a few hours ago called servo Buzz Control. I've used his method with my robot to great success. Perhaps you should download it and give this a try with your issue.
Update, I tried the servo programmer and it worked very nicely. I just set the dead time from 1 (most sensitive) to 3 (mid sensitivity).
It's very easy to do and only took a few seconds for each servo.
Cool! I'm glad this helped. Somethings it the simple things in life that make the most difference.