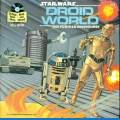
clintgarr75
USA
Asked
— Edited
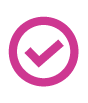
I was wondering, the way the Omnibot 2000 claws are set up, it seems a solenoid may be able to make them open with a spring acting to close them. Is this possible? and if so is it a good idea due to the fact that solenoids are usually high voltage and I can not seem to find a digital one, are they able to connect with the EZ-B? Please let me know if this is a good idea? Thanks.
Josh had an idea using small window door locks. You will have to check to see if it will fit though. I tried and failed at using a smaller solenoid so I put it on the back burner. As far as the power is concerned, you can use TIP or MOSFET to switch it on. Rich made a tutorial on how to make it from scratch. He has a bunch of other tutorials as well here. (Second post this time Rich)
If you want a premade one you can find them on ebay. Here is one of them.
There are lots of 12v Solenoids available. http://www.mcmaster.com/#solenoids/=ophk6i. Also some 5 volt ones like https://www.sparkfun.com/products/11015. Some have springs on them others do not. They are great for momentary activities, but you typically don't want them on long because they are battery eaters.
Oh wow, so I would connect a regular motor to the SMD MOSFET and then the MOSFET to the EZ-B and it will be able to control the motor just like it would a servo? This may be the answer I have been needing, I could just replace the motors in the Omnibot and connect MOSFET's to all of them and just use the gears that are already in the arm for it to move. I was thinking I would have to replace everything stock with servo's like D.J. and Mr. A did. will this work?
If using DC motors and you want them to both go forward and reverse you should use an H-Bridge. Let us know your operating voltage and the how much amperage the motor pulls and we'll recommend a good h-bridge.
Using the MOSFET I can not just plug the Motor directly into the EZ-B?
The MOSFET is controlled by a small low voltage 5 v that is supplied by the EZ-B ports. The MOSFET switches a larger voltage that is used by the motors and is not supplied from the EZ-B.
@clintgarr75, dschulplus is correct. For the purpose you describe you need the H-bridge for forward and reverse. For higher current motors, more than one mosfet (I think 4 per motor) are used in the H-bridge circuit. A single mosfet will give you one direction switching. I know Im oversimplying it but essentially you need an H-bridge. I'm sure someone in the forum can recommend one for the stock omni robot.
Ok, the arms of the Omnibot are really getting to be very tricky to work out, does anyone know a really simple solution for the Omnibot 2000 arms that doesn't require a degree in electrical engineering to figure out?