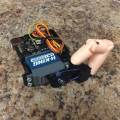
overserved
USA
Asked
— Edited
Problem:
- Current finger sensors require to many moving parts to make
- Personal problem is I know very little about programing but I am learning
Solution:
- Paint the interior of the finger tip with conductive paint
- Connect conductive paint to a lead wire and run to circuit board
Future Advantage:
- If the finger sensors work and are reliable, then rigging the entire Inmoov should be extremely easy and reliable
Do you think I should buy
- Carbon Conducti paint
- $14.95
- Surface resistivity: approximately 114 ?/sq for one coat (~1 mil)
- https://www.amazon.com/MG-Chemicals-838AR-15ML-Carbon-Conductive/dp/B01MQ4F1T5/ref=sr_1_3?ie=UTF8&qid=1538855760&sr=8-3&keywords=conductive+paint
- Silver Conductive paint
- $55.00
- Extremely low volume resistivity of 7.6X10-5 ?cm c.https://www.amazon.com/gp/product/B01MCXW1Y1/ref=s9_dcacsd_dcoop_bw_cr_x__a_w
It looks like in your design the finger joint is squeezed flatter by pushing against (grasping) an object, and this closes a make-break contact with the paint on the inside of the finger joints. Afik the Inmoov is printed from rigid plastic so this would require quite a bit of force- you wouldn't want to shake hands with it. Instead how about this: Cheap computer keyboards used to be made using the conductive foam packaging for circuit boards and components inside the keys. As a key was pressed the electrical resistance of the foam was reduced allowing current to flow and the keypress registered. The foam then raised the key back into position to await the next keypress. Why not use the same system for pressure sensors where-ever needed. You could then program varying levels of pressure (fingers) for different tasks by controlling the maximum allowed or minimum required input from grip sensors.
Hello @rocketsmith
My design does now work with physical pressure. It works with sensing conductivity through a surface. The outside of finger tip is the surface. The inside of the finger is a ridged space that has been coated with conductive paint with a lead wire running to a circuit board. This means when my finger comes closer to the Inmoov finger it will register its proximity to the surface. In return I can easily map an entire neural network though out the Inmoov.
I appreciate how well the conductive foam works but I want to try something different. I also want to map out 90% of the Invmoov body.
Thank you for taking the time to write and I appreciate your feedback.
Here is a simple example of carbon conductive paint in action.
I see now. It's not conductivity that is registering but body capacitance, like an old AM radio. You should be able to achieve the same effect with any conductor that you could apply inside the finger, like copper tape or metal foil. It's a question of cost vs ease of application, which ever is best for you. I'd try using their library and code with some sheet metal like aluminum foil to see if I could cut costs and get started right away instead of waiting on shipping. If the metal foil works, try reducing the size of the area necessary to determine the minimum size that will work, to see if a finger segment is too small, before buying the paint. If you do test it this way please report the results.
This is pretty cool. Have you considered making this a user tutorial? Check it here: https://synthiam.com/Tutorials/UserTutorials/
Hello @DJ Sures
The main problem is time. I'll try and document to process to make it easy for others with a proof of concept video but my time is extremely limited!
PS When are you going to make different size servos and improve your shipping price to the states? A dead silent servo is gold! Thank your for such an amazing platform.
Best wishes
Thanks for the kind words!