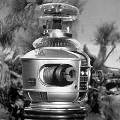
steve.neal
Australia
Asked
— Edited
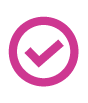
I am planning to use a couple of Sabertooth / Kangaroo combos in my B9 project. The robot will be stationary and will be powered by a plugged in 12 volt power supply. I seem to remember something about the synchronous regenerative properties of the Sabertooth requiring a battery for somewhere to channel the feedback voltage to. My question is how is this connected? Do I connect the battery in parallel with the power supply or can I forget the battery and use diodes to stop the back flow. I have searched on line but cant seem to find what I'm looking for. Am I on the wrong track altogether?
Even if the power supply is the same voltage as the battery if it is not a charging power supply then my guess you will need a way to isolate the battery from the power supply. That is if you are going that direction......
I assumed the battery and power supply would have to be the same voltage and I guess the power supply would charge the battery even though I don't need it to, Its just there to absorb the return energy from the Sabertooth and keeping it from damaging the power supply when the motors are slowed or reversed. I've seen others like Dave S have used this combo on his AWESOME B9 with much success but I cant work out how the regenerative property's have been handled.
Even at the same voltage your power supply would not charge the battery properly... Since your power supply is not a charging type power supply it has no way to recognize when the battery is fully charged... At this point normal smart chargers would switch to trickle charge mode... You charger would keep pushing amps into the battery until it shorted out or possibly causing a fire...
I am going to say without absolute certainty so you may need to confirm... Using an appropriate diode to prevent energy bleeding back to the power supply might be a viable route...
Hopefully Dave will chime in on this topic. I did find this though
https://www.dimensionengineering.com/appnotes/atxguide/atxguide.htm
My power supplies are not like the one pictured though, they just have 12 volt / 8 amp output terminals. As Richard said, it appears this method will over charge the battery.
Hi Steve, welcome the EZB forum from down under! I first gotta say that one of the best experiences of my life was spending 3 weeks doing adventure touring in your country and another week down in New Zealand. You have some of the coolest areas in the world to explore and some of the nicest people!
Anyway, enough of that!
Thanks for the nice words about my build. I'm real proud of the way he's turning out. I'm currently having fits over developing my arms. Many false starts and lots of wasted money bit I'm getting close to a working model.
I know you're not here to hear me spout off about how good I am so lets talk about your question
You certainly do need a battery wired in parallel with your power supply and it does need to be the same voltage. So if your using a 12v DC power supply or an ATX (or similar) computer power supply DE recommends you use a sealed lead acid 12V battery - Minimum capacity of at least 1.3Ah. There is a nice tutorial on DE's Sabertooth 12x2 web site on how to wire up a ATX power supply. If your using a DC power supply it can be wired up the same way except you don't need to add the resistor they show. Here's a link:
Using a SyRen/Sabertooth with an ATX (or similar) DC power supply
Now, I was fussing over the fact that the battery would keep the Sabertooth powered up in my my B9 when I turned him off. I had no switch between the two and I didn't want to add one that I had to reach in and turn off each time I powered down. The Sabertooth/Kangaroo would stay energized till the battery would drain down to zero. That causes some problems with the Kangaroo X2 when I powered up the next time. I also didn't like the way the battery backfed the power supply even though DE said "that's just the way it is". eyeroll Well,... not in my B9.
I built a circuit that lets the EZB turn on the power when I start up ARC and connect to my robot. When I power down the B9 it naturally opens and disconnects the battery. Problem solved.
In this circuit I also added blocking diodes to keep the back feeding problem from happening. Here's a link to a thread I started discussing all this and the schematic I finally came up with to do it all.
Turning off a Sabertooth
Edit: Looking at my schematic it looks like I forgot to draw in a diode between R1 and the tie to Q3 with the band facing away from R1. This would block the Sabertooth from pushing it's Regen power back into the circuit from that way.
Hope this helps! Do you have any pics or stories you can share about your B9? I'd love the see it all!
Have fun! Dave Schulpius
Dave,
I hope I can explain this right... I don't think it is an issue in your bot since he is stationary, so moving him when powered off wouldn't be an issue, but I thought the Sabertooth could be damaged if it isn't connected to a battery (or somewhere to send it's regen power) and the motors connected to it are rotated (like pushing a powered off robot that has wheelchair motors, which then act as generators and the Sabertooth tries to send the voltage to the battery).
Am I wrong, did you not worry about this because your range of motion isn't enough to make it an issue, or does your circuit take this into account?
Alan
Also Steve on a different subject; You're going to face a few challenges when you start setting up your Kangaroo. Make sure you have a TTL to USB connector so you can get into the software on the Kangaroo from your laptop. You may want to make a few changes to the way it works, check settings and test run it directly from your laptop. Your also going to have to make sure your drive circuit is complete before you try to start it up and do an Auto Tune (at least on the workbench for testing). At a minimum you'll need to have hooked up your motor, power supply and a stable feedback device attached to your DC motors shaft. These feedback devices can be either potentiometer (I found that only a 10k will work for me) or an encoder.
When the time comes let me know if I can help. Dave Schulpius
Here's a cheap USB to TTL adaptor:
TTL to USB Adaptor
Alan, thanks for the interest and insight. I've read that the Sabertooth will do it's regen trick when it's breaking. I read this to be when the motor was slowing down to a stop but I may be wrong. Even so, in my B9 it is possible to move the waist, radar and hip motors attached to the Sabertooth when he's powered down. Much like you mention in your example of pushing a wheelchair around. In my circuit the path back to the battery from the Sabertooth is fully open and the switches work to turn it off because of the diodes. So, even if the sabertooth does regen powered down when I push the motors it will dump into the battery. I'm not really a circuit guy so it's kinda like magic to me. Here's a simple drawing of my concept:
I've not had any problems with damage and the circuit works perfectly as I describe. cool