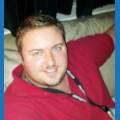
jstarne1
USA
Asked
— Edited
Hi im trying to get squeegee moving , I have wired the 4 individual signal pins and then a wire as a enable as well. I soldered one wire accross the enable pins. I followed the steps as described in the turtorial and went as far as to swap out for a different h bridge.I did a short video and tried different things. Can others post pics and possibly video for comparison. It must be somthing simple but im scratching my head at the moment. After trying just the Movement Panel and. Single pwm , I tried setting a pwm for each pin. It seemed like whatever I did there was no change :/ hmm. Please watch and help , I don't ask for second opinions often.
https://www.youtube.com/watch?v=UKJmHQ2MsKg&feature=youtube_gdata_player
USING 4 WIRE H-BRIDGE you need pwm channel for each motor and one of the input pins for each motor you need DIR control high or low ,depending forward and reverse with out a dir control you robot will start turning and never stop PWM is only for speed ,not direction look up the info on the datasheet for L298 it says the same thing in the truth table
I always breadboard all my designs first before adding to a robot.,i can check current,stall current and torque to see if its enough and most is easy to do in your design you only need a h-bridge ,ezb ,motor and may be a small wheel to show witch direction its going and check stall current.
h-bridges are easy for me ,i mostly design my own,but sometimes i buy them like L298 ITS EASY AND CHEAP TO USE
Josh, are you still having trouble with this? I'm using several H-bridges but not driving two motors in tandom. I can snap a few pics of my setup or take a video if you still need it. Can't do it till Friday though.
I haven't been able to watch your video due to tech problems on my end. Is one of your wheels even turning at alll or is it just spinning slower?
Bump Josh,
Maybe you overlooked my reply and question.
I've been thinking about your problem and am still happy to help if needed.
Did you ever have the wheel motors working correctly or did this happen from the first time you started up EZ Robot and your robot? If it worked for a short time and then one side locked on and the other side stopped working like you show in your vid you may have burnt out this motor controller. Voltage flyback from DC motors when quickly reversed is a real problem. I burnt out 3 H L298n H Bridges like this and after that happened they acted just like your vid shows.
Are you getting lights turning on and off on the motor controller board as you toggle the movement panel?
I know you're an advanced user so please don't be offended with my suggestions but:
Double check your wiring, continuity and if you have the ports set to the proper wires in ARC.
Make sure your enable pins and wires from the motor controller are attached to a digital signal port pin on EZ-B
You only need one PWM control if you have have the two rear outside enable pins jumpered (soldered) together. Assigned in ARC to either of the two pins.
You can have a PWM control assigned to each of the two rear outside enable pins but you must NOT have a jumper between the two pins. That way you can control the speed of a motor attached to either side of the motor controller independently.
Try wiring the two motors to one side of the motor controller (in Parallel) and use only one PWM controller for that side. You may find that one motor hogs the load and the other one lags wiring it up this way. With only one PWM control available there is no way I know of to balance the load.
Try installing Digital port controls in ARC and assign them to each port you have a motor wire attached to. You can try to toggle the motor on and off (ONE AT A TIME) in each direction that way. You will need e a PWM enable wire hooked up as mentioned above with a PWM control in ARC for that port and set to over 25% or so to get the motor to move.
Good luck and let me know what you find. Dave Schulpius
ITS seems like DAVE said might help also if you are getting it to spin in one direction its seems you may not have both enable pins together or one channel got fried
OK so I swapped the h bridge for a new one I bought on eBay. However I cannot get motor one , that's enable pins one and 2 to reverse. I connected the motor direct to power and it reverses. Then I tried the same motor of the number 2 motor channel and it will reverse. Crap! So somehow I have a half blown channel. Motor one output apparently won't reverse. Grr. OK once again setting this as side till tommorow as equipment not working properly pretty much infuriates me. I do not believe this is related to ezb because I tried three different sets of pins with the same results.
Josh, Sorry your having these problems. I know how frustrating this can be. You have better judgment then me though. I wish I could just put it down and walk away. When this stuff happens to me I usually screw with it till I either get it working or blow it up. More often then not I blow it up. sick
Anyway, take a deep breath and try starting at the beginning. Unhook both the motor and h-bridge from EZB.
After you have un-hook the the Hbridge, test the lead end that attaches to it from EZB to see is your getting the proper voltage you expect when you operate the control in ARC. Don't reattach the h-bridge till you start getting the proper voltages you expect.
At this point you should have set the digital ports up in your control in ARC. Double and triple check to see if they are correct. Don't use a Movement Panel yet. Install a Set Digital control for each port and toggle them on and off for your testing. Make sure your PWM slider is control installed and assigned to the proper digital port. Also make sure it's slid up to 100% for testing. That will give you a full 5vdc. (later when you do hook up your motor you will only start out at 20%. You don't want your motor taking off and ending up in your back yard). eek
I found when I was having these types of trouble I needed to reboot EZB. For some reason I would have a port signal that would either be locked on when ARC connected or would not work. A complete power down of everything (h-bridge, EZB board, ARC and the computer) and a restart would usually fix it. Kind of like in Jurassic Park when they had to send people over to the power house to shut everything down then restart to get the computers working. Lets hope you don't get eaten when you try it.
I also noticed at one point that when I toggled one of the Set Digital ports on and off I would see two ports turn on and off in the movement panel. Very confusing so I just deleted the Movement Panel for now and used the Set Digital control for testing. One other thing to try is to write a script to: turn on the PWM to 100%, turn on one port, sleep for a few seconds and then turn it off. Do this for each Digital Port in question and watch it with your tester.
The other thing that always worked for me was to move the problem lead(s) to a different EZB digital port. Heck, move them all and reassign them in ARC. Same as above, I would have a port signal that would either be locked on when ARC connected or would not work. I have a feeling that it has something with the way ARC saves the state of it's ports when you save and shut it down, but I'm not sure. New ports starts everything new.
Once you have your digital voltages turning on and off as expected hook up your h-bridge and test the motor side with your tester. Do not hook up your motor yet. Do your tests the same as above. This way you know everything is working to this point and may have found where the problem is.
When all is working good install a Movement Panel Control and assign your ports. Test at the motor connection points on the h-bridge to see if your getting the proper voltages turning on and off when using this control. If not you know the problem in in the Movement Panel control and how it's set up. If this is your problem try moving the port assignments around in the Movement Panel control to see what happens.
Don't attach your DC motor till all voltages are as expected. When you finally do attach your motor start slowly. Only run your PWM at about 20% first and slowly slid it up to 80%. Don't use your Movement Panel yet. Turn on and off with the Set Digital Controls. Make sure your PWM is set to 20%. MAKE SURE you turn off one control before you turn on another. Wait a second between motor forward and reverse changes. When that's working properly move to your Movement Panel Control and see how that is working. AGAIN, DO NOT change directions quickly yet. Make sure your PWM is set to 20%. Move in each direction then stop, wait, then move in another direction.
Remember to breath deeply, test, test, test before attaching a DC motor and move slowly. Make sure your PWM is on or you will get no readings and don't change the direction of an unprotected h-bridge quickly. Fly back voltage from the DC motor will burn it out. This may not be an issue on a smaller DC motosr but the bigger ones will destroy your control circuit. I don't know where the cutoff point is or at what size motor starts to be a problem. Pololu has some great little H-bridge (motor controllers) that have nice over voltage and reverse voltage protection. Average cost is between $35-$65 USD.
Good luck and have fun! Let me know if this helps.
Dave Schulpius