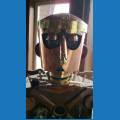
irobot58
After looking over the vast amount of Forum threads on modified servo positioning it seems that good ole resistance pots are very popular. I am using many modified servos with DIY gears with my project and would really like a good easy positioning fix. Has anyone tried using "hall effect" solutions? Cheap! Small!.....I am thinking of mounting/gluing 8 or more small magnets on one of my gears and having a hall device "signal" the EZ-B and with a running script to count, therefore knowing fairly well where the arm/elbow/shoulder is. Besides knowing where the linkage is I am thinking what with "slipages" it would be also good to have a "home" position with a second hall device, and with a script always bring the linkage back to a home spot! Does the SDK offer counting? Insights and comments are welcome!
Also this is a link of someone who has hacked a modified servo and embedded an IC AS5040 a 10bit encoder for feedback.
AS5040 10bit encoder
Insights and comments are greatly welcome!
Humm, A Hall Effect sensor should be a lot better then a resistance pot. It measures the magnetic field around the conductor and can be monitored just like a pot as it has three terminals. A sensor voltage is applied across two terminals and the third provides a reading of the current being sensed. I wonder though if the small voltages and currents we work with would be a problem. A sensor with current amplification may be needed. One problem I can think of is bleed over of other magnetic fields from energized wires laying around it. This can be a huge problem in the little bots most of us are building. But on some of the bigger robots (like my B9) this may not be a problem if the sensor can be places away from other wires or shielded in some way.
As far as counting, I don't think ARC supports optical encoders. I looked into encoders a while ago and hit a dead end. However, maybe a breakout board that converts the optical count to digital may be available. That way EZB may be able to recognize the changes in digital or ADC ports and a creative script may be written that would be able to read them. But you wanted simple and that is not simple.
Always good advice Dave!
...just to be clear the AS5040 is still Hall effect! the round magnet placed inside the hacked servo has two polarities which the 5040 counts..how cool is that! If the EZ script offers a counting solution then the position of the modified servo will be accuratly known.........I am hoping people can offer comments on the "homeing" idea. I know Rich has mentioned the issue of slipage before...Have you noticed problems of not returning to the correct spot with your B9? and have to recenter.
Yes, I have seen "slippage" and B9 has stopped at the wrong place. Haven't really delved onto "why" it happens. The way I solved the problem is to have a "centering" script and have the movement script call that script a few times at the end. That way he always lines up where he should in the end. However it would be nice to avoid all that.