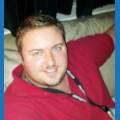
jstarne1
USA
Asked
— Edited
Hey I was playing around looking for more info but was unsuccessful. What's the torque rating at 6 volts and can these servos have multiple exact positions? For example could a continuous rotation servo be used for radar by setting a end/stop point in each direction left/right? Thanks!
Found it on the web ; Dimensions: 41x38x20mm Weight: 38g Voltage: 4.8 - 6V Working Temperature: 0 - 60 degrees Celsius Speed: 0.15sec / 60 degrees Torque 3.5Kg/cm @ 4.8V
Ok I found a "heavy duty" continuous rotation servo with metal gears. 121 oz in , that's 7.5 lbs in torque! So if your bot has a big butt this doubles your torque over the servo in the kit.
http://arduino-direct.com/sunshop/index.php?l=product_detail&p=131
If your in.USA and need a servo/wheel combo quickly they have them too.
I ordered 1 from Hobbyking that is a modified servo that does 6 turns. I plan on using that way but it may be able to change it it continuous. they are rated at 694 ozf/in ! wow !
J.W.
Yhey guys you have to understand how a servo works and what the modification is.
A normal servo has a "POT" variable resistor attached to the output shaft. the electronics inside the servo generate an error voltage from the shaft position relative to the input pulses. this voltage drives the motor which moves the output shaft. The result is that the shaft will home in at a position indicated by the pulse train. By the way, most servos have a pot that only moves about 180 degrees, thus the output shaft usually are limited to about 180 degrees as full rotation. In EZ-Robot, DJ assigns a range of 0 to about 70 to represent this full range.
a "Modified" servo has the "Pot" disconnected from the output shaft and usually set to a fixed point about halfway round. Thus it is sort of indication a shaft position of about 1/2 through the 180 degrees. However, since the output shift is not attached, the electronics inside the servo still generate the error voltage relative to the input pulse train.
thus, if the pulses indicate a 1/2 way position, the voltage output would be 0, and the shaft does not move. If the pulse train tries to send the servo to a position less then 1/2 way the the voltage would move the motor backwards, which the voltage increasing the further away from 1/2 way you send the input request. Since the out put shaft is not attached to the pot, the error voltage stays and the shaft rotates continuously.
Thus, the "modified" servo has no endpoint. no way to turn a certain number of times and hit an end. OF course, a genius can somehow modified the connection of the shaft and the pot to come up with a solution. ie. a precesion 10 turn pot somehow attached to the shaft, can be used to set up a servo to run as a "normal" servo but have any position in the 10 turn range be the match to the pulse train.
One can also somehow get a variable resistance attached to whatever your moving, and have that feed back to the electronics, instead of the internal pot, you can get what you want. I've been working on that myself on the robot I'm working on. ON the back burner for now.
DrWass2
@ww321 please link that servo you bought that had a very high torque rating , that would be an excellent option for my waist of omnibot 2000 left and right twist.