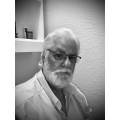
smiller29
The Birth Of The XR-1 DIY Robot
Introducing the Updated XR1 and the New XJ-5: A New Class of Hobby Robots
The XJ-5 robot platform, available at Robots Builder, stands out for its user-friendly design, emphasizing accessibility and ease of assembly. Designed to make robotics more approachable, the XJ-5 is meticulously engineered for easy 3D printing and assembly with standard parts like servos and bearings.
Our goal is to simplify the building process so that enthusiasts and robot hobbyists of all skill levels can engage in constructing their own robots. We've invested time in perfecting the design, ensuring that users can quickly move on to the exciting tasks of programming and teaching their robots using Synthiam ARC. The XJ-5 is highly customizable, featuring a variety of hands and heads to allow personalization of each creation. To encourage a collaborative and open community, we're proud to announce that the XJ-5 is entirely open source, inviting users to contribute, modify, and share their innovations globally. Get ready to embark on a journey of creativity and exploration with the XJ-5!
For more information, check out Robots Builder.
As a creator of the XJ-5 and our other XR series, I will be leveraging the Synthiam ARC platform for robot control, and I hope others here will join me in developing an ARC project to support the XJ-5 robot. As of January 9th, 2024, we have started posting files for 3D printing. Meanwhile, we are developing documentation and the above website, so please check back regularly.
My goal is to have a walking, talking, listening, and seeing robot the size of a small child using ARC and its various skills. As I progress, I will be sharing more about my efforts here.
Now, let's dive into the project focusing on the new and improved XR1, the XJ-5, which I have been designing and building over the past year.
As a young enthusiast, I loved the movie Short Circuit and fell in love with the Johnny 5 robot, inspiring me to create a similar robot. It was not designed to replicate the original Johnny 5. About a year ago, DJ suggested preferring a robot with wheels or tracks over a bipedal robot due to the complexity of making them walk, a challenge I am familiar with from our XR2 project. But hey, that's another story.
Now, in May 2025, I've almost completed the assembly and will start implementing ARC and the AI brain I've been working on to support ARC. More updates will follow.
I have started building the torso from the hips up, as shown in the pictures below. The shoulders are not fully installed because I'm waiting for the correct screws to arrive. Please excuse the messy workbench.
To support the robot, I have designed a set of boards with ARC firmware that will connect to the onboard PC, which will be situated in the middle of the chest.
The above board will be mounted on the backplate between the two shoulder sockets and connected to the USB hub that will be connected to the PC. Two more USB cables, along with servo power, run down to the boards in each hand. The USB camera and headboard will be connected to the PC's other two USB ports. ARC will run headless on the Windows 11 Pro PC using RDP for remote connectivity. Additionally, there is an MPU connected to the main board that I plan to leverage with ARC.
I have added the shoulders and arms down to the wrists, and they appear to be strong and capable.
I decided to create a Johnny 5-style head for my build featuring two cameras. Here is the completed head. I have added six more servos to the build for the eye flaps, bringing the total count to 50 servos. It includes a directional mic array and ultrasonic radar for enhanced audio and visual capabilities. For sound, two speakers are mounted in the head with an audio amplifier.
I have also decided to add an option to the XR-1 to support a 5-inch touch display, as shown below.
The display will provide more options for operator interaction using ARC remote controls.
I have created both two and three-finger claw grippers and human-like hands, providing versatility in interaction for the XR-1.
Pretty cool robot! How tall is it?
@Jeremie, He is about 105cm or 42 inches tall I think he is currently 44DOF at this point depending what you do in the head it could be more.
The current design will have a very small but powerful Windows 11 Pro PC on board with USB hub connecting an Arduino Nano in the head and Nano in each hand and two Mega Pro's on the back for everything else. It will also have other sensors.
Very cool. Great work. I took a look at your BOM, I am glad you used hobby servos and gave links to AliExpress . Every time I go to build a project it’s just buy a dozen of these $1500 dynamixal servos
Nice work smiller29
Anyway section by section part by part he is being uploaded, we should be at 80% by end of week less the head and hands only.
The head is very close to being completed. The hands are going to take a bit longer as we are working to make a strong functional set of hands and with the child size they are smaller so it creates a challenge. We have been working on many concepts but have not decided which one to use at this point.
We have added a link to SYNTHIAM on the website for a software solution for the XR-1 so I hope you get some added traffic to your site.
I am hopeful that the Arduino Mega Firmware is going to work on the Mega Pro Mini without having to change it.
My testing starts today I hope if I find issues I can get some help from DJ to fix things to support these boards because our project is depending on them.
Looks really exciting. Thanks for sharing. Good luck with the roll out.