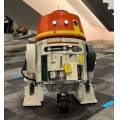
PRO
Davidaharrison
Canada
Asked
Chopper Update, Sabertooth Movement Panel
Thanks to the new max speed and dead zone settings for Joystick, Chopper is up and around. Before limiting he max speed he was crazy fast I could barely control him, Set to 60 in the max speed setting right now. Still a fair bit I need to fine tune but overall its coming together.
Oh wow ! thats awesome. Great job. Details!
That movement looks real sharp! What else do you think would help with your needs? From the video it looks better than perfect
. But you’d know from the controls.
It's not quite as smooth as I'd like for turning, seems to be times when turn delays slightly which isnt present on front back movement. Can't quite pin down why, was getting late last night so decided to call it. I'm thinking of exploring Uart connection options vs the simplified serial. Not sure if that's a factor here.
Overal super happy with it, first Con is end of October so still have a month to finish things off and add some more features.
This is how the joystick works. Is it the spin on spot or direction that you find difficult?
Thanks thats very clear, the spin on the spot. Maybe it's a dead spot setting issue, it's the spin on spot that seems to have the delay.
Now that I see this I'm wondering if it's the area defined as spin. Maybe it's coming in as a forward/left vs a spin left and it's causing a delay sometimes. Looking at it you would barely notice but controlling it sometimes you feel for a second like it just doesn't quite register. Maybe when I get the smooth response it's when I'm right on track with the spin area but sometimes I hit the forward/left?
The deadzone also defines the spin. Try increasing the deadzone
Here's how the deadband looks..
Just got a chance to do some driving in a more open space and it seems to be that the left motor is not turning as fast, causing a fair amount of drift. What I'm seeing is the Fwd/Right works well but Fwd/Left is almost straight. I think that's part of why the spin does not quite seem right.
I'm thinking I need to trim it somehow for a little more input on the right.
Here's a video showing stick input and the robots reactions. You can see sometimes there's nothing. Its almost like a stall, but with 24v and 150W motors I should be good, I would think. Its a 2 x 12 Sabertooth so 288w normal, 576w peak, the bot weights in at under 60lbs. https://youtube.com/shorts/8p652dEyXOA