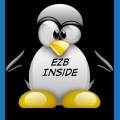
Darathian
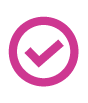
Since I know some of you have used the Sabertooth and Kangaroo I figured I would ask opinions.
I have decided on the Parralax Arlo base for my next robot chassis. I will use the caster's from parralax.
I will most likely be using the Sabertooth and kangaroo combination for motor controller/PID but I am not decided on this and open to suggestions.
I also find myself in a heated mental debate between the wheel/motor combination from parralax or the Zagros Rex motors and wheels combined with the Sabertooth/Kangaroo.
Item 1:
One of the key items for me is how well the encoders between the two different motor/wheel sets works with the Sabertooth and kangaroo.
Item 2:
The other item floating in my mind is the ground clearance between the two motor/wheel sets. It seems at least to me that the Zagros wheels would provide more ground clearing but since the base plate of the chassis provides stability to the base platform I am not really sure if using the Zagros motors are feasible.
Item 3:
Since I am going to build a body, arms and head on top of the base the torque and weight carrying ability is important.
Item 4:
I need to be able to control both the position and speed of the motors at the same time. For example example I should be able to have to robot move lets say 1 feet at a certain speed.
I know this is kind of an open ended questions but if anyone have used any of these wheel/motor combinations please provide your 2 cents as it relates to the items listed above.
I appreciate any comments or insights you guys can provide.
Just a caveat... I bought an Arlo base and although an awesome base, I have to tell the encoder implementation is crap.... For one thing the encoders don't sit tight on the motor output shaft... One of mine got chewed up in the encoder board.... They lasted all of 10 minutes... Maybe you will have better luck... Personally I have my money on DJ's camera based indoor navigation system coming soon....
If you do buy the base get the aluminum wheels, I wish I had of. The plastic ones are a bit fragile....
Probably not your cup of tea, but the iRobot Create has all that implement in one neat little robot chassis... Encoders, bump sensors, wheel drop sensors, wall detector, edge sensors.... I have several and they are a really great self contained robot chassis....
The only things I have on order is the plastic base itself and the casters.
I like that the encoders on the Rex motors are attached to the motor versus the disc based encoder that separately attaches on the parralax motors.
The other aspect that makes me lean towards the Rex motors and wheels is the wheels on the Rex does not need to be inflated.
I saw a number of posts on the parralax forums about the wheels losing air and needs to be inflated with a hand pump every so often.
If I do end up going with the parralax set it will be the aluminum ones.
The other aspect of the Rex motors I like is adjusting the height of them could easily be done using a shim between the mount plate and the chassis base.
Assuming my math is good it seems the parralax motors have more torque though.
@Richard R
How did you find the parralax swivel casters. Do they move freely?
I agree with you the Zagros stuff is actually really good.... Funny enough, I have a few of their bases too... I don't think you will be disappointed with the power output of the Rex motors.....
The parallax casters are great.... High quality for sure.... So are the motors, but as I mentioned the encoder implantation is crap... The Rex encoders are contained in an end cap whereas the Arlo encoders are in the open and like what happened to me, easily damaged...
The Arlo base and casters plus the Rex motors sounds like a great combo to me....
I was looking at the encoder assembly again and it seems that it depends on the internal teeth of the encoder ring deforming against the output shaft hence gripping the output shaft tightly.
I have to agree with you that it seems an somewhat iffy design especially with the shaft rotating and potentially vibrating.
If the ring is plastic and depending on the teeth size and plastic type the grip on the shaft may not last.
I am not sure what the distances are between the ring and encoder module sides but it cannot be much.
It seems there is an element of luck involved on how tight that encoder ring assembly would be.
Thanks
@Richard R
Have you used the Rex motors with the EZB and a motor driver to control the motors.
If so what issues did you run into?
Thanks