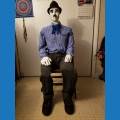
Andy Roid
This goes out to the guys who build bigger robots.
I have taken standard servos and stacked them to build a "Spine" for my new project. I find the rotational servos weak in the bearing area. I plan on adding a plate with an additional ball bearing to give more strength to the shaft area. Other than buying larger heavy duty servos, has anyone else modified servos to add strength? Any ideas?
I also made a heavy duty lever which seems to remove some flex in the lever servos which helps in this area. I will build wider adapters for the back and bottom of the servo to spread the load when clipping or stacking the servos together. This may also help.
I am requesting other members ideas and opinions to be able to build a more ridged "Spine for my project, but not add a lot of weight.
I will update my project progress with pictures soon.
Ron R
Hi Ron, I totally understand wanting to beef up a servo. Usually standard servos have a challenge with a big lateral load. I faed this problem when designing my B9 Robot arm. If you dont have your heart set on scratch building a support there is a off the shelf solution. ServoCity sells something called Servoblocks. They come in different styles and have them to fit either Hitec or Futaba standard servos. Here's a cut from the web page listing one style:
This is what they look like:
Here you can see how I used one to support the heavy wrist and claw of my B9 arm:
Go here to shop, choose and buy: ServoCity's ServoBlocks
Hope this helps, Dave
WOW ... Thanks Dave. I can see this idea can resolve my problem. My only concern is weight. I will look at it online for the details. This maybe a concept for a 3D printed one incorporated into my spine assembly?
I like your Buddy in the lower left corner of the picture too.
Ron R
Glad this helps Ron. I don't know much about strength of 3D printed plastic so I cant comment intelligently on that. I'm a metal guy but I do know that ABS plastic is very strong and may work. However I think you may get too much flex from plastic to rigidly support a lateral load properly. That's just a speculation though.
Yah, Skye is a fun little friend. She seem to always be there when I need a smile. I didn't even notice her in this pic till after I took it and looked at it later.
Good luck and have fun. Dave
Dave
This is a picture of my test layout. The lower most servo is the one we talked about. I may use the same idea on the lever servos also. This will also have a pelvis of similar design. Legs will be like the arms.
I will post a project update soon.
Ron R
Hi Dave and Skye,
I looked at the servo City's site. A lot of good stuff which I will be ordering. What I don't see is spline shafting. Do you know any where I can get some. I was going to put out a request to the community for blown up servos (LOL) for the gears with the spline. As you see I have little space to work with and weight is a big concern. I have to finish the spine and build a pelvis and legs. This means mounting 10 more servos to operate the hips and legs. All the weight is in the servos and mechanics around them.
By the way, I can't wait to see the next video of your Big Guy's progress. It has been VERY enjoyable watching your dream come true.
Thanks for your help,
Ron R
Hi Ron,
Thanks for the very kind words. The "Big Guy" is a passion and dream coming true. Skye keeps me company a lot of the time during the long hours I spend in the shop working on him. Your concept is very cool. I cant wait to see how it progresses. I'll be watching!
I'm not sure what you mean by spline shafting. If you mean a way to extend the shaft away from the servo spline ServoCity does have many ways to do this. Look at the following links for a few of the many options they have:
www.servocity.com/html/servo_to_shaft_couplers.html#.VdDbM_lViko
www.servocity.com/html/set_screw_shaft_couplers.html#.VdDbePlViko
www.servocity.com/html/bearing_mounts.html
www.servocity.com/html/servo_shafts___couplers.html
I was looking for the actual spline used on a servo. Many of the flanges and adapters I have use the i.d. spline used on the servo. I was trying to get a length of the o.d. spline to join existing flanges together etc.. If it is unavailable, I will try using the items you showed me from the web site. Thanks for the additional info. I will keep you posted as to my progress.
Ron R
Ron, what brand servo are you using? Most follow either the HiTech or Futaba standards. Here are the specs on both:
Futaba servo Splines: www.servocity.com/html/futaba_servo_splines.html#.VdFMOflViko
HiTec servo Splines: www.servocity.com/html/hitec_servo_splines.html#.VdFMuvlViko
Good Luck. Dave