Asked
— Edited
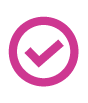
What do you all think? Is it possable to use one pot for two devices for feedback? I have one motor I have one pot attached to it so I can send position feedback to one of EZB'S ADC ports. I'm hoping I can just tap off the sensor lug and run that to another device. That device is already attached to EZB and shares a common ground. It's' a Kangaroo x2.
The resistance value will be identical on both ADC ports.
Thanks doc, however I won't be using two ADC ports on the EZB, just one. I want to run the other lead from the pot to the kangaroo. This way I would have one cable going from the pot to the king rule and another going from the pots to the ADC of EZB. Very sorry if I wasn't clear about that.
@Dave ....I thinking it should work and of course coinciding the ADC read with one of the two devices. I am presuming the devices are not on at the same time! Also paying attention to the input voltage for the ADC port not exceeding maximum. Perhaps a quick breadboard setup running the devices on at a time and measuring the output voltage would ease any anxiety
That's just it, they will both be on at the same time performing their own things. I like the breadboard idea I was going to get the multi meter out tonight anyway.
OK, the answer is YES! As Doc said the resistance value was identical on the signal pin of both device's ADC ports. Here's the way I wired it;
I needed to give the pot a 5vdc and a ground on the two outside of three lugs. The center lug is the connection that reads the difference in voltage as the pot's knob is turned. I got the 5vdc and Ground from the ADC port of the Kangaroo X2. So, I have: 1). 5vdc output wire (red) from Kangaroo directly to one outside lug of the pot 2).Ground output wire (Black) from Kangaroo directly to other outside lug of the pot (Kangaroo & EZB have a common Ground also) 3).Signal wire (White) from Kangaroo to the middle lug of the pot and I've spliced a second white wire mid way that runs over and connects to one of the Signal pins of a ADC port on EZB.
When in install a ADC Value Monitor in ARC I can see the value go up and down as the Kangaroo X2 controls the position and speed of my motor from the same pot.
Now, ya may wonder "what's the big deal"? Well, The way I control my B9 waist movement is I send commands from EZB to the Kangaroo X2 with Serial Commands. The problem is that the V3 EZB only has one way serial commutation. The Kangaroo cant send back info to ARC for Speed or position. Once the command goes out EZB is blind and doesn't know anything. I want EZB to be able to send a serial command to the Kangaroo X2 at a certain point of the rotation of the Waist motor to start slowing down to a stop. Till now I've been relaying on manual timing with the Sleep() function in a ramping script to ramp down. That wasn't always working well on mutable moves. This will aid me in speed ramping down to zero easily and at the exact and proper time. Using the ADC value that EZB is reading from the same pot the Kangaroo is using for speed and position I can now start that ramp down script just at the proper moment. Using Variables and a little math in that script I can have my B9 waist move to any point at any speed at any time and always speed ramp up and down smoothly at the proper time. Yaaaaah!
Now I need to get the script working properly. Shouldn't be much of a problem as I've already got most of the code written for other motors in the B9. Thanks for letting me bounce this off you guys. I hope this will help others that need to do something like this and need this type of feed back with no two way serial commutation on the V3 EZB. I understand the V4 will have this feature and that will be great. However there will be lots of classic V3 EZB's still out there.
Sorry Glen, Gotta give this one to Robot Doc. He got my head gears turning first. However you helped a lot
No worries Dave!
I am happy to help in any way and this is ALL good for others as well
I luv it when satisfaction is realized!
and of course a big thank you to Robot-Doc !
Dave, I didn't want to start a new thread since I have a question relating to the same topic. I'd like to know what encoder/potentiometer you used with your kangaroo set up? Am I correct in understanding you are using it to turn your robot's (awesome robot by the way, my wife and I were laughing at your videos the other night) waste but not movement, is that correct? I think I would have to have some sort of encoder instead of a potentiometer since my application is drive wheels but would like any input you could provide. Regards Matt De,ing
Hi @Mat,
Glad you are enjoying my vids. I'm a true armature and just muck through them.
The pot I'm using is just a cheap multi turn from The Robot Shop. I have one installed for waist rotation positioning and one for Radar positioning. They sell a real expensive one and a real inexpensive one: www.robotshop.com/en/phidgets-multiturn-rotation-sensor.html
www.robotshop.com/en/dfrobot-rotation-sensor-v2.html
I see you've been struggling with the Kangaroo X2. Have you read through my other threads where I've been working through a few issues I had? If not take a look:
synthiam.com/Community/Questions/5374
synthiam.com/Community/Questions/5304