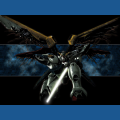
budel0
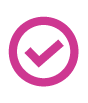
Hello everyone,
For the last 6-7 months I've been upgrading my robot with a new drive system. A few weeks back I finally had all the parts to complete the upgrade. Then it started... The electrical problems... It doesn't work, then it works, then it stops working, then I use different motors, it works! Then one of my motors starts smoking after a test drive.
I'll give some more information first... So the robot. It uses 2x 540 brushed RC motors, 7.2v, 45 turns, maxes at 8100 RPM at 4.29 AMPs. These motors drive a 6wd differential gearing system.
What I did with this design is simply said, I merged 2 rc cars in to one, by removing the back end of one of the cars. Due to this the front motor receives more load than the rear motor, eventhough they are all connected via gears and axles. Not sure why, maybe the middle differential requires a look, possible a gear problem.
To control the motors I'm using a Saberthooth 2x25A motor controller, I have set it up so each motor channel is controlled seperatly, reversed the polarity on one of the motors and control the two channels with the same signal.
To power this monster, I'm using 3x 2s 4000MAh 20c lipo batteries. No problems here(I think), one of them is a bit puffed, but they all work.
Now the actual problem, the system works, but when I add resistance to the motors(making it drive on the floor) they heat up fairly quickly, not as fast as the other ones I used. Before one of my motors started to smoke, I could drive around for about 5-6 minutes. The motorcontroller flashes the error led sometimes, this could mean to much current, low battery voltage or overheat, but there is no heat, the batteries are charged and the motors are only 9A together.
Could some one help me resolve this problem, I'm dieing to continue with my other "mini" projects for this robot. And it would be nice to see my hardwork drive around for longer than 5 minutes.
Hello @budel0,
Your batteries are OK, same with the motor driver, both are rated accordingly. I'm not certain of your mechanical layout though, it seems that you have 1 motor driving the 2 front wheels, and another driving the 2 back wheel (going reverse). One thing to keep in mind is that motors often don't turn the exact same speed as each other and also don't go the same speed going forward versus backward. Add a geared linkage in there and you will have a system that may be quite different from front to back. You be getting one motor trying to push the other to be fast enough, which is putting undue load on both motors.
One way to fix this would be to measure the speed on the back versus the front with a tachometer (or encoder) and then trim the speed in software by adding a certain percentage of PWM until both speeds match. You could also slow the system down by putting lower rpm motors in order to get more torque. The issue might very well be that the motors just aren't torquey enough to carry the weight of the new chassis.
Another issue could be mechanical binding of the gears and linkages, do you see any of the gears not meshing properly or if it's harder to spin the gear than usual? A simple shot of lubricant might do wonders as well. Keep an eye out for missing teeth and gear sections flexing as well, you don't want either of those.
P.S. The puffy LiPo is on it's way out, you'll start to see diminished capacity very soon, it'll get harder and harder to keep a charge. You may want to look at a replacement.
@skater_j10 Thank you for helping me. There is only one mechanical part in the system which could be causing problems and that is the middle differential, connecting the front, middle and back wheels creating 6wd drive. It's the only part which I changed to have a different purpose.
I never though about the difference (the deviation from the ideal specs) between 2 motors that should be the same. And because they are connected via gears and axles they receive more load. Though your solution to it will work, I like to keep it simple. So I'm proposing to remove one of the gears from the middle differential, by doing this the front and back motor aren't connected any more. Would this help? Or would it stay the same? Make it like a push pull or would it be the same?
Anyways, I'll have to take it appart... Completely, damn I hate the guy who designed it (me T.T). I'll also continue my queste for high torque motors that are the same size.
Something else to consider during your design stage of testing would be to use a bench dc power supply that can also display the amount of amps used when running the drive motors.
@Robot-Doc Well I've always wanted one, so a few months ago I had build one. But it's max is 3A.. I figured that all the electronics I'm going to make myself would either be small and low in power consumption and thus I would not need a PSU that would give like 10A...
But thanks for the tip. Maybe in the future I'll make/get one with more power.
Hello again guys,
After spending 3 hours on disassembling, checking parts and other things I've found that there is nothing wrong with the gears and linkages. There was no damage or lack of greas in the gearboxes. After I had removed all the gearboxes and had only the wheels left... I found that only these took "force" to rotate them.
Thinking back to just a few weeks ago, when I installed aluminum parts that required the removall of all the wheels, I noticed that when I tightened the wheelnuts to much it generated friction somewhere between the wheelmount and the coupling that connects the wheel to the gearbox. Which made it even hard to turn the wheels by hand. So 30 seconds later the wheels could spin with ease and stayed spinning for a while.
Once I assembled everything back together, I took it for a test drive. This time there where no red flashing LEDs. And with ease it could drive around. The motors weren't heating up and it could drive with very little throttle. It could actually drive around on one motor.
So I'm calling this issue resolved unless someone else has something to add.