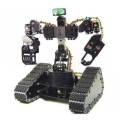
robotmaker
USA
Asked
— Edited
I design a circuit awhile back and sold many pcb;s with my design My design is that you can use 4 wire instead of 5 wire to control the l298 h-bridge board,second you can control PWM seperate for each motor and add a brake if wanted
Its a 2 wire design,i dont know if it will work with EZB it should,it has one direction control and one pwm control and can be set up with total of 3 wires too with 2 wire for direction control and one pwm control ,and if needed another wire for safety brake or overload (stall) brake.
way it set up now it uses 2 wire per motor for direction and en pin for pwm control
my circuit is under $3 in parts
Would you be willing to share this design or sell it? I would be interested and would need a sketch and list of components.
yes i will , when you open the zip go to pwm to h-bridge and use only part of the circuit uses a nand gate and inveter circuit it will have 4 lines out you dont need the h-bridge chip HP4081
You dont have to use the enable pin if you dont wont too and CD4071 ,that was for a dual circuit control.
it will have 2 pins pwm and dir ,only 2 chips is needed CD4069 (INVERTER) and CD4081 (NAND GATE)HBRIDGE.zip
To control need a digital output for DIR and one for PWM
This design gives 2 PWM control if needed or tie both PWM together to use 3 pins total for 2 motors ,you need 2 circuits
sorry i made a mistake on the chip that was used you only need half of the CD4081 (and) gate and CD4069 pwm says the same to have 2 wires and 1 pwm control for DIR for the first motor you use in pin 5 on U2 for DIR1 and for DIR 2 you use pin 9,output pins to l298 is pin 3 of U 2 to l298 pin 5 and U 2 pin 6 TO L298 PIN 7 and the same for other gate going to L298
I guess i need to fix the circuit to make it easy for others
DAVE here is the simple circuit and can easy fit on a small radio shack protoboard h-bridge1.zip
pretty simple circuit ,needs 2 very low cost chips CD4069 and CD4081 it for a dual h-bridge controller L298 or others,can be used for one motor or 2 motors or with PWM control on both motors
Thanks Fred! Very helpful and appreciated.
next looking at the pins on different L298 H-BRIDGES and how to hook them up correctly,since others having problems.
AND there make a few different versions of the board,one DJ sells,one i have ,pololu type and some on ebay for about $5,even sparkfun sells a different type
Mine as 4 leds 2 reds and 2 greens
I love the pololu brand. Everything and every level you could ask for. Very sturdy and well self protected. Not to drive any business away from ARC but the 2.5 amp motor controller they sell seems easily destroyed by DC backlash current. I've burnt up 3 of them. When I switched to the pololu VNH5019 Motor Driver Carrier and VNH3SP30 Motor Driver Carrier MD01B I have had no problems. They work over a wide input voltage range and have a nice over voltage and reverse voltage protection system.
The Motor controller EZ Robot sells is great for light demand motors but I fear they burn out if you use a larger motor and reverse directions quickly. It's happened to me. Another way to get around this is to build a diode board that will drain off to ground the voltage spike sent back from the DC motor when direction is reversed quickly. I built two into my robot just as added protection. I'm anal and hate to repair things that shouldn't have been broken in the first place.